This article covers everything you need to know about floor stacking vs. pallet racking.
In it, you’ll learn:
-
What floor stacking and block stacking are
-
How each compares to pallet racking
-
How to choose between each warehouse storage method
-
Tips for stacking goods
Let’s dive in!
Quick Summary
Don’t have time to read the whole article? Here’s a quick summary of the main points.
- Floor stacking involves storing loads and pallets on the ground without stacking them on top of each other
- Block stacking involves storing loads and pallets on the ground while stacking them on top of each other
- Pallet racking consists of steel vertical and horizontal beams which hold pallets off the ground
- Floor stacking and block stacking work best for operations that don’t move their materials often, don’t use First-in, First-out (FIFO) inventory management, and don’t have the capital to invest in pallet racking
- Pallet racking is a good option for handling time-sensitive goods, such as in Last-in, First-out (LIFO) inventory management. Additionally, it helps protect goods from damage, makes better use of storage space, and is flexible enough to handle many types of loads
Floor Stacking & Block Stacking: An Overview
Wondering which two types of stacking are used in the warehouse?
They are:
- Floor stacking
- Block stacking
Let’s go through each.
Floor Stacking
What Is Floor Stacking?
Also called “single stacking,” floor stacking is where pallets are placed directly on the floor, side-by-side, without stacking them on top of each other.
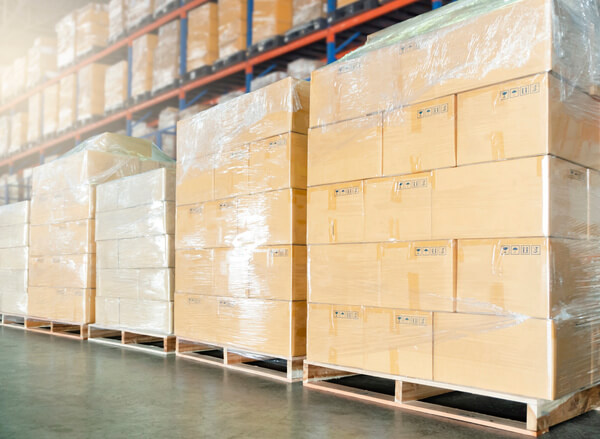
Pros of Floor Stacking
-
Inexpensive. Floor stacking doesn’t require any equipment or infrastructure set up. Instead, pallets or loads are simply placed on the floor
-
Easy to adjust storage layout. If you want to change how you store your goods, you’ll only need to paint or tape lines on the floor and/or hang signage
-
Potentially high storage density. You can create rows of storage as deep as your space permits
Cons of Floor Stacking
-
Relatively poor use of warehouse storage space. Floor stacking takes up a large amount of floor space, leaves vertical space unused, and can cause excessive honeycombing and accessibility waste
-
Limits visibility and access to products. It’s easy for your products to become buried, especially when there are mixed SKUs
-
Increased risk of damage to goods. Because there’s nothing in between pallets to protect them, frequently moving loads can damage surrounding products
-
Only works with Last In, First Out (LIFO) inventory management. Your oldest goods will be placed further back. Thus, you can only easily retrieve your last-placed load
-
Limited to certain floor types. Floor stacking is only suitable on asphalt or concrete since these floor types are solid enough to support multiple stack pallets. Gravel or dirt floors are too uneven and unstable
What Is Honeycombing in a Warehouse?
Honeycombing refers to the loss of usable storage space.
Here’s how it happens:
When products are removed from their lane positions, they leave empty spaces behind.
If those empty spaces cannot be filled, you have wasted warehouse space.
Honeycombing is a big problem when storage lanes are earmarked for particular SKUs.
When the SKU is removed, and there isn’t an identical SKU to replace it, you’re left with a warehouse space that you could’ve used for storing other items.
This becomes costly for warehouses since you can’t rent out and charge fees on the unused open spaces.
So, how do you reduce the effects of honeycombing?
One way is by mixing your SKUs so they don’t stick to a certain lane.
But this might not be possible with floor stacking, as you will greatly reduce your ability to select particular SKUs without having to move other SKUs out of the way.
Floor Stacking Applications
Floor stacking is best for operations with the following characteristics:
-
Those that handle non-perishable/non-time-sensitive goods using LIFO inventory management system
-
Those that handle uniform products
-
Those that don’t need to move loads often
For example, companies that handle home appliances often use floor stacking.
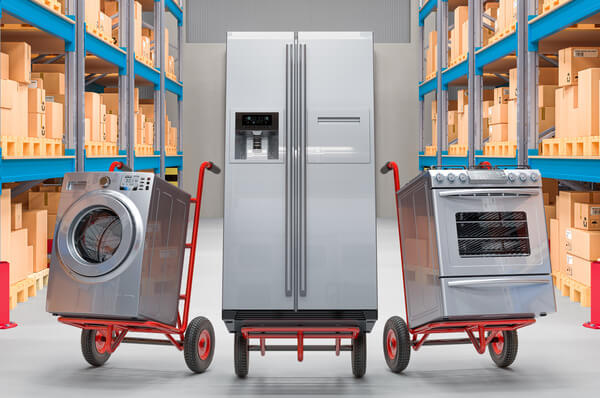
Block Stacking
What Is Block Stacking in a Warehouse?
Also called “block stacking,” “pallet stacking,” or “double stacking,” block stacking is where pallets are stacked on top of each other and tightly side-by-side.
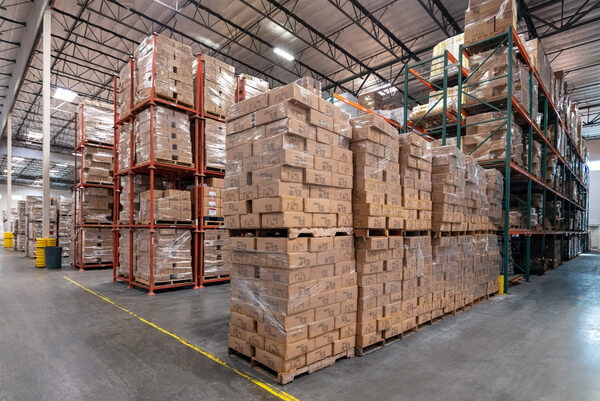
Some people use floor stacking and block stacking interchangeably, but they’re different.
Whereas floor stacking doesn’t involve stacking pallets on top of one another, block stacking does – usually 2 to 3 pallets high or until the maximum height is reached.
When placed in rows, each pallet is supported both vertically and laterally.
Thus, they have some protection against toppling over.
How High Can Pallets Be Stacked?
There is no maximum pallet stacking height maximum height, per se.
Instead, the stack must be secure, stable, and not interfere with other infrastructure, like sprinkler systems.
That said, national fire code authorities and insurance companies do offer some guidance for the maximum height of pallet stacks, including:
- Don’t stack taller than 6 feet
- Group in stacks of 4
- Keep 8 feet of space between stacks
Some other things to consider when setting a safe maximum block stacking height include:
- The strength and crushability of the materials. In other words, how much the load weighs and how much weight it can withstand from above
- The pallet condition. Weak and damaged pallets can easily collapse and should not be used
- The ceiling height. Along with any clearances that must be maintained, such as sprinkler systems, HVAC ducts, and lighting
- The type of weather (if stacking outside). Rain, high humidity, and wind can compromise the integrity of the pallets. This can result in them being able to handle less weight while remaining stable
- Any other applicable safety standards. All warehouses are not created equal. Any particular hazards or safety requirements unique to your business should also be considered
Pros of Block Stacking
-
Makes better use of vertical space. Any way you can use up vertical space is a great way to lower your storage costs. And block stacking is more efficient this way than floor stacking
-
Cheaper than pallet racking. If costs are a major concern, block stacking allows you to improve your usable storage space without capital expenditures on racking
Cons of Block Stacking
-
Less accessibility. Removing bottom pallets will involve removing the top pallets, which can result in a lot of wasted time. This makes floor stacking not ideal for First-In, First-Out (FIFO) inventory management
-
Risks of injury and product damage. Stacking loads invariably increases the risk of them falling over. Especially so with block stacking, since loads are not separated and supported by a pallet racking structure
-
Doesn’t work well with fragile loads. The loads underneath must be able to take the weight of those on top. Otherwise, you risk damage and collapse
Block Stacking Applications
Block stacking is best for operations with the following characteristics:
-
Handled goods allow loads to be stacked on top of each other
-
Those that use the Last-In, First-Out (LIFO) inventory management system
-
Operations that lack the budget to invest in pallet racking and have plenty of space to store pallets
For example, paper manufacturers often use block stacking to store paper rolls on top of one another in between production and shipping.
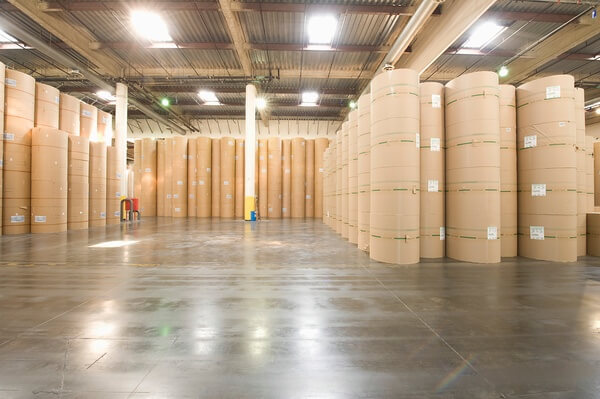
Additionally, block stacking can be used in addition to pallet racking.
For instance, this can come in handy when goods only need to be stored temporarily in a certain area until they can be sorted and dispatched.
Pallet Racking: An Alternative to Stacking
Instead of storing materials on the floor and/or directly on top of each other, you can use pallet racking.
Let’s go through what you should know about pallet racking.
What Is Pallet Racking?
Pallet racking consists of a vertical frame and horizontal beams held together with locking hardware and upon which pallets are stored.
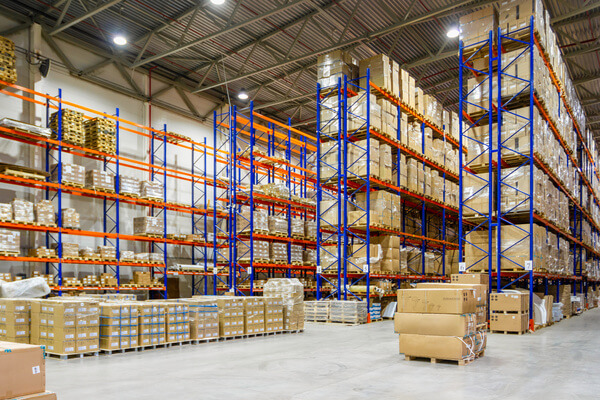
Operators use forklift trucks or other material handling equipment to load and unload the pallets from the racking.
Types of Pallet Racking Systems
Pallet racking systems come in a few different varieties.
Let’s go through the main ones.
To learn more about the different pallet racking systems, see our warehouse racking guide.
Selective Pallet Racking
Selective racking is the simplest type of pallet racking.
It’s basically a large, sturdy shelf with a high load-bearing capacity.
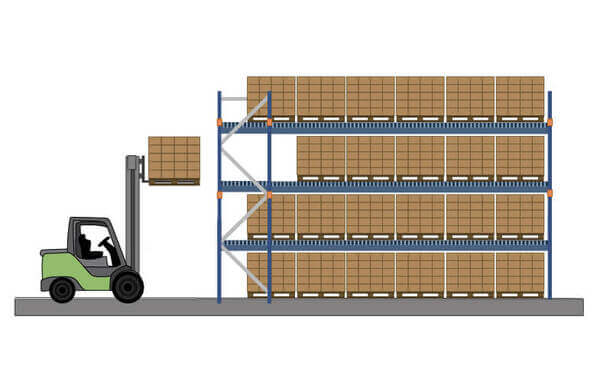
This system can handle a large variety of product types, enables easy access to pallets, and works with First-In, Last-Out (FIFO) or Last-In, First-Out (LIFO) inventory systems.
Pallet Flow Racking
Pallet flow racking uses angled horizontal beams equipped with rollers.
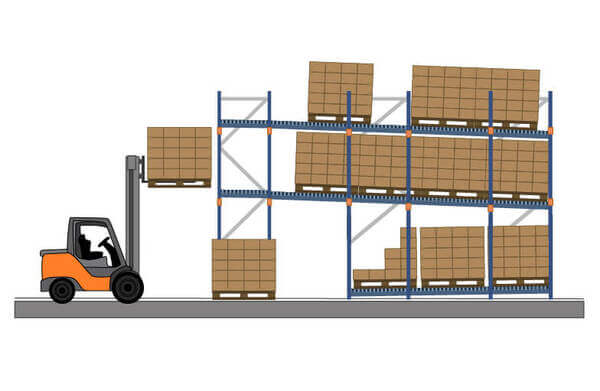
Here’s how it works:
- Forklift operators load pallets into the high end of the roller tracks
- Gravity moves the pallets toward the low end
- Then, when the first pallet is removed, the others advance one position
Pallet flow racking is best for operations that handle time-sensitive products, like food and beverages.
Push-Back Racking
Push-back racking is much like the shelves in a convenience store.
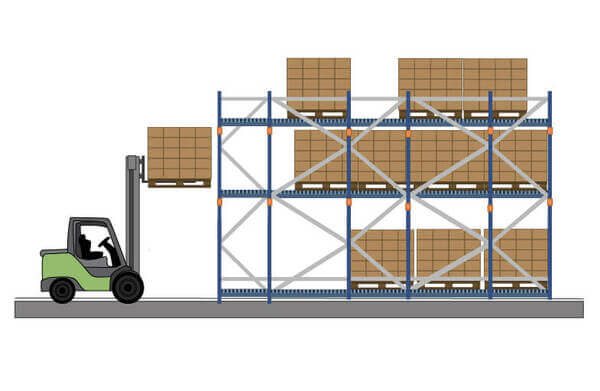
It’s angled towards the front so that when product is removed, product from behind slides in to replace it.
Like pallet flow racking, the advantage of these systems is that operators don’t need to reach into the racking to retrieve each load.
Drive-In and Drive-Thru Racking
What makes these racking systems unique is that forklifts actually drive into the racking (as opposed to staying only at the face of the racking).
In drive-in racking, operators enter the racking at one side, placing each load at the back of the racking:
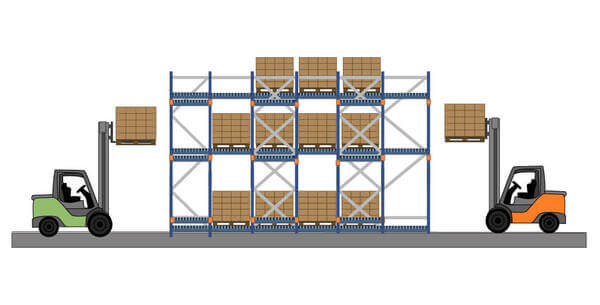
In drive-thru racking, operators can enter the racking from either side to place or retrieve pallets:
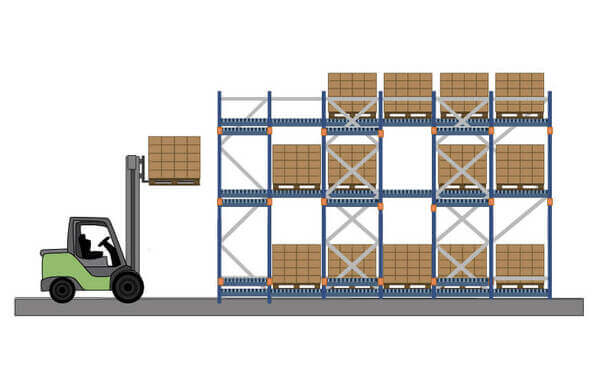
The former system is best for LIFO inventory management.
And the latter is best for FIFO inventory management.
Cantilever Racking
Cantilever racking consists of columns and arms that jut out.
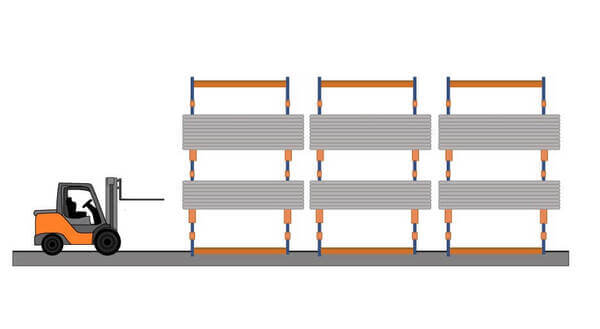
They’re ideal for oversized and awkward loads, like lumber, piping, and furniture.
Pros of Pallet Racking
-
Flexible and versatile. Pallet racking can be designed to accommodate nearly any SKU, load, or pallet type or size. They can support different weights and can be modified to accommodate inventory changes
-
Supports different inventory management systems. Different types of pallet racking can handle First In, First Out (FIFO) or Last In, First Out (LIFO) inventory management systems
-
Increases storage density and makes better use of vertical space. Expanding horizontally is more expensive than expanding vertically. Pallet racking helps take advantage of that space. In fact, using pallet racking can improve storage space by up to 40%
-
Improves order picking efficiency through better selectivity. Product selectivity is how easily operators can retrieve specific pallets from storage. Pallet racking is the easiest way to place and retrieve loads
-
Enables better product organization and easier inventory rotation. Pallet racking eliminates the need to move multiple pallets to retrieve one on the bottom as happens in block stacking
-
Improves safety and reduces product damage. By providing more separation and support for loads, pallet racking reduces the risks of loads toppling over if unevenly stacked or if forklifts hit them
-
Clears up floor space. Floors can become easily crowded when using floor or block stacking. Pallet racking gets goods off the floor and makes maneuvering easier
Cons of Pallet Racking
-
Requires greater upfront investment. If using floor stacking, you may be able to get by with a simple manual pallet jack. But to use pallet racking, you’ll need some type of forklift or other material handling equipment
-
Prone to damage. Floor stacking and block stacking can increase the chances of damage to the load, especially from forklifts. Pallet racking takes away that risk, but the risk of damage to the pallet racking itself remains. Using pallet racking protectors and bumpers can help reduce the amount of damage, however
-
Requires periodic inspection and maintenance. This is required to ensure the stability and safety of the pallet racking structure and workers. But it does cost time and money
Pallet Racking Applications
Pallet racking is ideal for operations with the following characteristics:
-
Those that deal with perishable goods, as it can support FIFO inventory management much better than floor or block stacking
-
Those that handle goods that can’t be stacked on top of one another due to the risk of damage
-
High turnover operations, since pallet racking makes it easier to add and remove loads than floor or block stacking
For example, we use pallet racking to store forklift attachments, battery chargers, and spare components like engines.
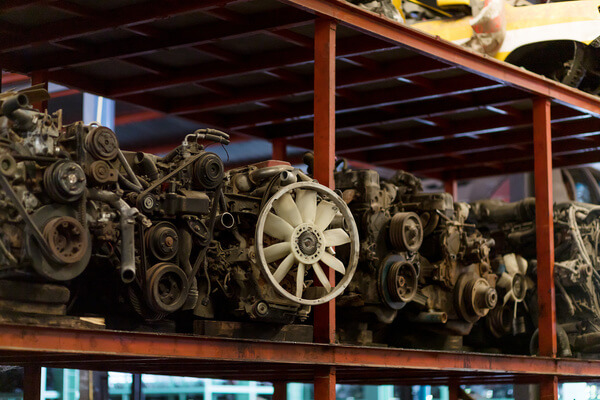
These are all loads that must remain accessible, can’t be stacked, and would be prone to damage if left stored on the ground.
How to Choose Between Floor Stacking and Pallet Racking
We’ve covered a lot of the pros, cons, and applications for the various types of pallet stacking and racking systems.
But let’s try to make it clear which is best for your needs by going through the top considerations.
How Often Do You Need to Move Pallets?
If you don’t need to move pallets often, floor or block stacking may be the right choice for you.
The more often you need to move pallets, the more you risk damage to the surrounding ones.
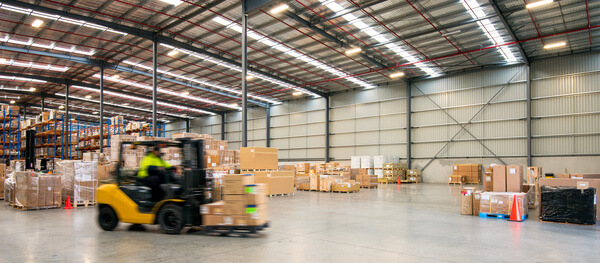
Thus, long-time storage with occasional movement is best for floor and block stacking.
Are Your Products or Materials Stackable?
If your loads can’t be stacked, you’ll need to use floor stacking or pallet racking.
For example, items like home appliances or forklift attachments can’t be stacked and may be best stored on the floor or protected up in racking.
Wide items like lumber, piping, or furniture can benefit from cantilever racking, which is designed for wide materials.
How Uniform Are the Products or Materials You Handle?
If all your pallets contain the same types of products and materials, you may be able to use floor or block stacking.
But if the products are different, you’ll have the problem of honeycombing.
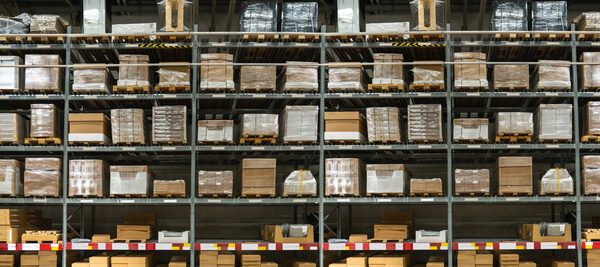
Thus, pallet racking may be a better option for handling multiple SKUs and loads.
What Inventory Management Method Do You Use?
If you don’t need to use First In, First Out (FIFO) inventory management (i.e. products that don’t expire), you can use floor or block stacking.
But pallet racking is ideal for Last In, First Out (LIFO) inventory management (i.e. perishable products).
That’s because pallet racking improves your product selectivity, which is critical for handling time-sensitive goods.
What Is Your Facility Layout Like?
In particular, consider your ceiling heights.
Pallet racking works best when you have lots of vertical height to take advantage of.
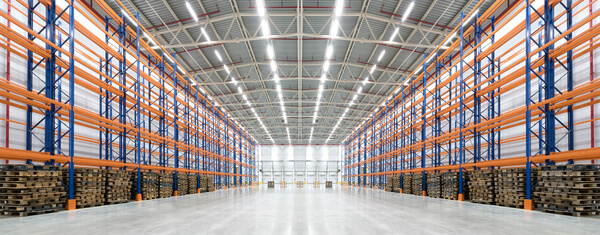
So, if your ceilings are relatively short, for example under 10 feet, then pallet racking may not be ideal.
In such a case, floor or block stacking might be your best option.
11 Warehouse Stacking Tips
Stacking pallets correctly is an important workplace safety concern.
So, follow these tips to help ensure you’re stacking pallets safely, maximizing storage space, and preventing damage to goods:
-
Ensure that pallets are free of damage and in good condition. Check that they can support the needed weight capacity of the loads they’re carrying. And regularly purge broken or damaged pallets along with those that have protruding nails or boards
-
Check for anything loose in the pallet. Wrap loose items with plastic or banding to prevent them from shifting
-
Keep loads with sharp edges away from aisles. This will help reduce the chances of employees cutting themselves on them
-
Only stack pallets that are uniform in size. This helps reduce the chances of the load shifting or falling. Keep stacks as even as possible. Make sure the weight is distributed evenly. And place heavier items in the center or across the bottom of the pallet
-
Don’t overload the pallet stack
-
Keep access space between the stacks
-
Keep adequate clearance horizontally and vertically. Never obstruct lights, electrical panels, ventilation units, sprinkler systems, or the like
-
Avoid putting pallet stacks in high-traffic areas. This reduces the chances of workers or material handling equipment hitting them
-
Do not place stacks tight up against the wall. This can create a breeding ground for pests like mice and insects to burrow into and contaminate your product
-
Avoid climbing or walking on pallet stacks
-
Only stack loads up to a safe height that maintains stability
Conclusion
That’s it: Everything you need to know about warehouse floor stacking vs. pallet racking.