This is your ultimate guide to maximizing your warehouse racking layout.
So if you’re wondering how to get the most out of your facility’s space, you’re in the right place.
In this article, you’ll learn:
- What warehouse pallet racking is
- The different types of racking systems
- How to choose and design a warehouse racking system to fit your needs
- How much pallet racking costs
- The best practices for pallet racking safety
- How to preventing damage to your pallet racking
Let’s dive in!
What is Pallet Racking?
Pallet racking systems are a storage method that leverages vertical space to store products and materials, whether single items or palletized loads.
Operators typically use forklifts to place and retrieve pallets and other materials stored on the shelves.
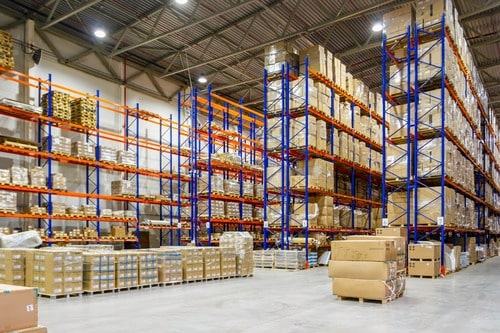
Pallet racking as a storage solution is extremely popular.
According to Frank Ceriello, vice president of sales for Aigner Index, some 80% of all industrial materials are stored on pallet racking.
What are the Different Pallet Rack Parts?
There are several pallet racking components that compose the shelving:
- Upright frames
- Horizontal beams
- Braces
- Baseplates
- Crossbars
- Clips
Let’s go through each one.
Upright Frames
These are the vertical steel posts that connect to the horizontal beams and bear the downward weight on the shelves.
Horizontal Beams
Beams mount horizontally to the upright frames – one in front and one in back – and compose the shelves.
There are two different pallet rack beam types:
- Step beams, which feature a lip on the inside of the beam and support crossbars and mesh decks
- Box beams, which do not have the inside lip and are compatible with wire mesh and safety bars
Braces
Braces are the horizontal and diagonal bars, generally welded to the uprights, that support the uprights and provide extra strength.
Baseplates
Also called footplates or footpads, baseplates connect the upright frame to the floor and are secured with anchor bolts.
Crossbars
Also called support bars, crossbars are placed between the horizontal beams to support pallets or materials and prevent them from falling through.
Clips
Also called universal safety drop pins, beam locks, or beam connector locks, pallet rack clips are small fasteners used to secure the horizontal beams to the uprights.
They prevent the horizontal beams from dislodging during loading and unloading.
What are the Benefits of Pallet Racking?
Pallet racking leverages the vertical space in your facility, allowing you to store more products and materials without expanding your horizontal footprint.
Overall, it’s a lot like the advantage of building a skyscraper instead of a regular building.
Thus, the benefits of pallet racking include:
- Saves money by lowering your cost per order
- Maximizes space utilization by taking advantage of vertical space
- Keeps you organized
- Helps prevent damage to products on the ground from pests, moisture, impacts, etc.
- Allows you to retrieve pallets more quickly and easily
Do You Need Pallet Racking?
While many facilities use pallet racking, it may not be necessary for certain applications.
For instance, many beverage warehouses use floor stacking (also called “block stacking”).
In this method, pallets are simply stacked on the floor in rows.
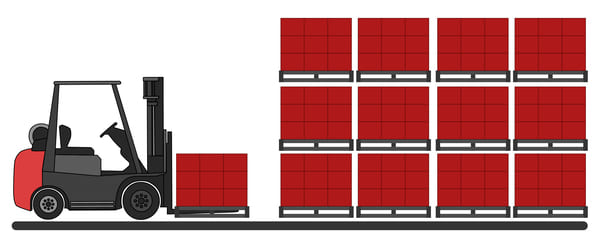
This system can be arranged to provide extremely high-density storage if the pallets or loads can be stacked directly on top of each other.
Generally, floor stacking works best for Last-In, First-Out (LIFO) inventory management.
What is Last-In, First-Out?
In a Last-In, First-Out (LIFO) inventory system, the first products or materials added are the last to be sold.
This method is less popular than FIFO.
In fact, the United States is the only country that allows companies to use this system.
Industries that use LIFO are typically those that sell commodities like bricks and stone since these materials are taken off the top of the pile and sold before the oldest materials are.
Advantages
- No cost for a racking system
- Opportunity for high storage density
Disadvantages
- Low pick selectivity – requires more labor to retrieve the right pallet
- High space consumption
- Higher risk of damage from impacts, pest, and moisture
If this storage method doesn’t suit your needs, keep reading.
We’ll cover the other types of racking in the next section.
Pallet Racking Types Explained
Overall, racking systems belong to two categories: low-density and high-density.
The advantage of low-density systems is that they afford better selectivity.
And the opposite is true of high-density systems.
What are Selectivity and Density?
Selectivity is how easily accessible products or materials are.
Certain types of warehouse racking layouts offer easy access (i.e. high selectivity) while others don’t allow order pickers to access products and materials as easily (i.e. low selectivity).
Density indicates the amount of goods or materials stored within a warehouse storage space space.
Different types of warehouse racking layouts will allow you to store more material (i.e. higher density) or less material (i.e. lower density).
High-density racking systems include:
- Double or triple depth racks
- Drive-in/drive-through
- Push back
- Pallet flow
Density and selectivity are related: The higher the density of storage, the lower the selectivity.
That said, let’s go through the common types of racking, their advantages and disadvantages, and common industries they’re used in.
Low-Density Racking Systems
Selective Racking
Selective racking is the most common type of pallet racking.
And it works with any type of forklift, so no specialized lift trucks are required.
There are two types of selective racking: one-pallet deep and double-reach racking.
We’ll cover each separately.
One Pallet Deep Racking
Selective racking stores pallets one deep.
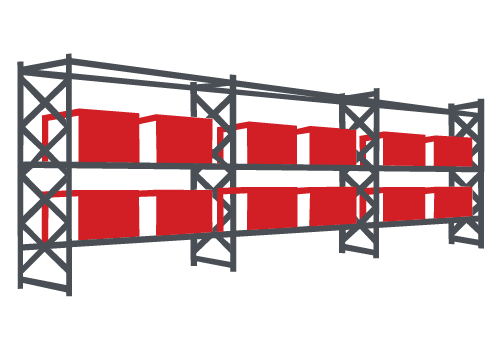
This system provides unobstructed access to each pallet within the system, making it ideal for the First-In, First-Out inventory systems.
What is First-In, First-Out?
First-In, First-Out (FIFO) is an inventory and accounting method wherein the first products stored are also the first to go out.
Overall, it’s the most popular inventory method used in warehousing.
Not only is it logical and simple, but it also works particularly well with perishable goods and other products that are subject to expiration or obsolescence.
Industries that often use FIFO include:
- Food and beverage
- Fashion and apparel
- Pharmaceuticals
- Electronics
- Cosmetics
Selective racking is well-suited to applications with low inventory turnover along with high product differentiation.
Advantages
- Low cost
- Flexible
- No specialty forklifts required
- Accommodates products of any volume, weight, or size
- All stock is visible and accessible
- Low risk of product damage
Disadvantages
- Low storage density
Common Industries
- General warehousing
- General manufacturing
- Retail
Watch this video to see how one-deep selective racking systems work:
Double-Reach Racking
Double-reach – also called double deep – racking systems are very similar to selective racking.
But instead of using one row, racking is placed two rows deep.
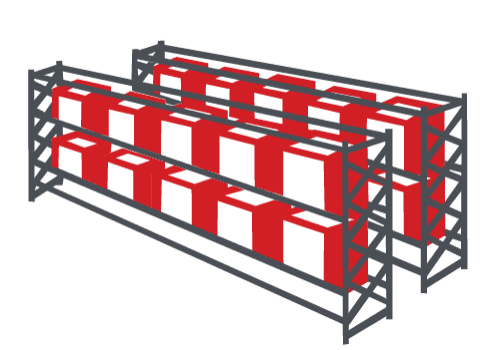
Racking could even be placed both back-to-back and two rows deep on each side, therefore maximizing density.
This system offers more pallet positions by reducing the number of aisles.
But it’s only compatible with First-In, Last-Out inventory systems.
Overall, double-reach racking is well suited for applications with multiples of the same stock.
Advantages
- Cost-effective
- Higher storage density
Disdvantages
- Reduces pick selectivity
- Specialty forklift required – which may add cost if not part of your current fleet
Common Industries
- General warehousing
- General manufacturing
Watch this video to see how double-deep selective racking systems work:
High-Density Racking Systems
Drive-In/Drive-Through Racking
With drive-in or drive-through racking, pallets are stored on rails in place of shelf beams.
These rails extend the length of the rack and allow forklifts to drive into the racking structure for pallet placement and removal.
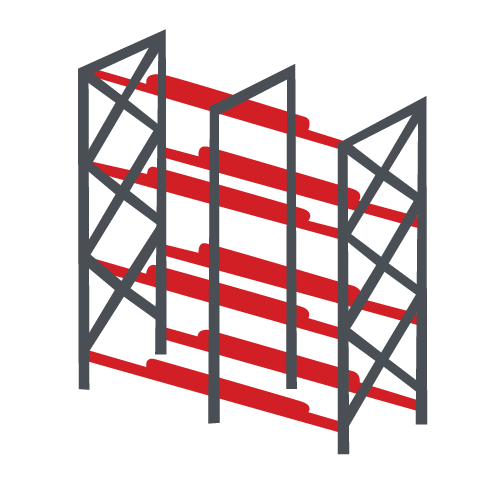
Drive-in racking is ideal for storing a limited number of SKUs with uniform pallet sizes and load measurements.
This allows for consistent load rail heights.
These racking systems work best with Last-In, First-Out inventory systems.
Advantages
- Increases pallet positions
- Requires less warehouse space
Disadvantages
- Reduced pick selectivity
- More opportunities for impacts or contact between forklift and racking
Common Industries
- General warehousing
- Freezer/cooler
- Retail
Watch this video to see how drive-in/drive-through racking systems work:
Push-Back Racking
Push-back racking consists of a series of nested, mobile carts which glide on rails.
The pallets are placed on the carts and stored in bays two to six pallets deep.
When a new pallet is loaded onto a cart, it pushes the other carts back.
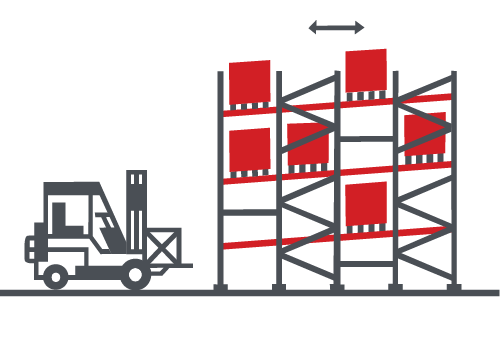
It’s much like soft drink coolers in restaurants, grocery stores, and gas stations.
As you pull a soda bottle out, a new one slides forward.
Push-back racking works best if you have little storage space and products that are consistent in size and weight.
This system is ideal for Last-In, First-Out (LIFO) inventory systems.
Advantages
- High storage density
- Reduces picking time
- Requires fewer aisles
- No specialty equipment necessary
Disadvantages
- More expensive storage option
- Potential for lost pallet positions due to the size of mobile carts
Common Industries
- General warehousing
- Retail
Watch this video to see how push-back racking systems work:
Pallet Flow Racking
Pallet flow allows up to 20 pallets to flow down an incline on a series of rollers or wheels.
The pallets are loaded on one end of the system and unloaded at the other end, making it optimal for First-In, First-Out inventory management.
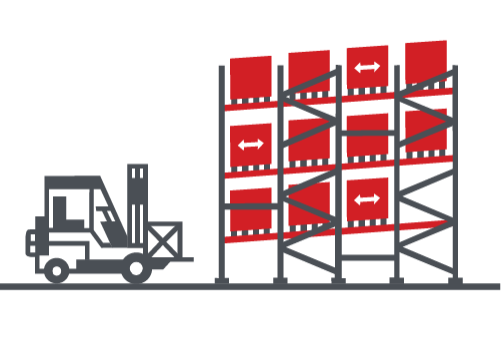
This system is an excellent option for applications with a very limited number of SKUs in large volumes.
It also works well for perishable or time-sensitive products.
Advantages
- Increased product selectivity
- Superior density
Disadvantages
- High expense per pallet position
- Potential for lost pallet positions – the system is on an incline which takes up more space
- Pallet flow system requires maintenance
Common Industries
- Grocery
- Retail
Watch this video to see how pallet flow racking systems work:
Cantilever Racking
This type of racking consists of protruding arms and is designed to hold lengthy materials, like pipes and wood.
Because the racking isn’t obstructed by solid vertical uprights, cantilever racking is well-suited for awkward or oversized materials.
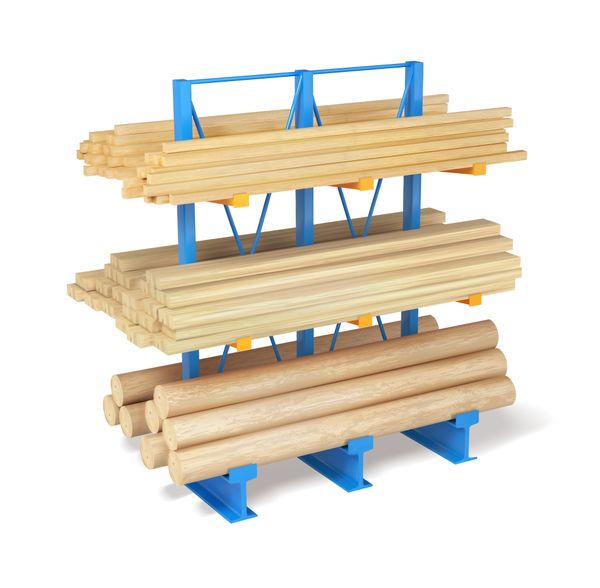
This system is ideal for Last-In, First-Out (LIFO) inventory systems.
Advantages
- Easy to install
- Easily adjustable
- Flexibility to store oversized or awkward materials and products
Disadvantages
- Requires wide aisles – unless using a specialized lift truck, like a Combilift
Common Industries
- Building supplies
- Metal shops
- Plumbing
- Furniture
Watch this video to see how cantilever racking systems work:
Pallet Rack Comparison Chart
We’ve compiled this quick pallet rack comparison chart to help you decide which option works best for you and your facility.
Racking Type | Ideal For: | Specialty Equipment Required | Storage Density | Inventory Management System | Cost |
---|---|---|---|---|---|
Selective | Products of any volume, weight or size | No | Low | FIFO | $ |
Double-Reach | Multiples of the same stock | Yes | Medium | LIFO | $ |
Drive-In | Limited number of SKUs with uniform measurements | No | Medium | LIFO | $$ |
Push-Back | Products consistent in size and weight | No | High | LIFO | $$$ |
Pallet Flow | Very limited number of SKUs in large volumes | No | High | FIFO | $$$ |
Cantilever | Oversized and awkward products | No | High | LIFO | $ |
How to Choose the Best Type of Pallet Racking for Your Needs
There are several important factors to consider when selecting pallet racking types.
Let’s go through each one.
Budget
Each type of pallet racking will cost a different amount.
So you’ll need to consider the cost per pallet of the system you desire.
We’ll cover the cost of warehouse racking in a later section.
Floor Space
How much room does your facility have?
Certain racking systems take up more room than others.
So you’ll want to be sure you select a system that’ll fit in your facility.
We’ll cover the steps to do that in the next section.
Material Handling Equipment
Some types of pallet racking require specialized material handling equipment.
For example, to be compatible with drive-in/drive-through racking, lift trucks require a special overhead guard.
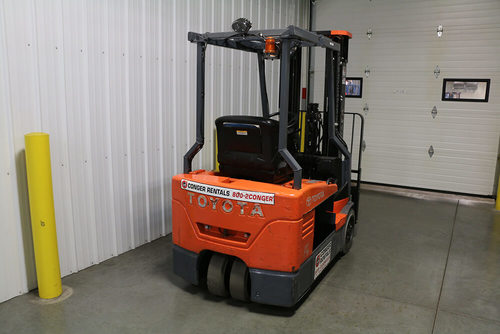
Additionally, if you plan to use narrow aisles, you’ll need a forklift with a small footprint for maximum maneuverability.
Flexibility
If you plan to handle a large variety of materials and products, your racking will need to be able to accommodate them.
Inventory Management
As we’ve noted, certain pallet racks are better suited for FIFO and LIFO inventory management systems.
So whichever method you use, you’ll need to make sure your pallet racking can accommodate it.
A Step-By-Step Pallet Rack Design Guide
When designing a pallet racking system, the goal is to fit as much material into the available space as possible while still allowing for enough room to quickly and easily retrieve items.
With that said, let’s go through how to determine the pallet racking layout for your facility.
Part 1: Determine Your Warehouse Racking Layout Design
Step 1: Measure Your Space
This will help you get clear on exactly how much square footage you have available to work with.
Step 2: Note Any Obstacles
Obstacles can include things like columns, doors, and mezzanines – anything that you’ll need to make space for.
Step 3: Determine the Best Location for Your Products and/or Materials
Fast-moving products should be placed near your shipping lanes so that it takes less time to retrieve and ship them. If you’re storing production materials, you’ll likely want to put them closest to your production line to cut down on pick times.
Part 2: Design Your Pallet Racking Sizes
Step 4: Identify the Dimensions and Weight of Your Pallets
Take the largest pallet you handle, and measure the height (load plus pallet height), depth, width, and weight. These measurements will tell you how much space you’ll need to accommodate your products and materials for storage.
Step 5: Determine the Frame Depth
According to Speed Rack West, the most popular pallet rack frame depths are 42-inch, 48-inch, and 36-inch.But keep in mind that you’ll need 3 inches of overhang on each end of the pallet. So to factor that in, simply subtract 6 inches from the depth of your pallets. For example, if your pallets are 48 inches deep, you’ll need a 42-inch deep pallet rack frame.
Step 6: Choose Your Beam Sizes
Per Stein Service Supply, pallet racking beam sizes are generally 4-feet, 8-feet, 9-feet,10-feet, or 12-feet.You’ll use the width of your pallets and how many you plan to store side-by-side to make this determination. Just keep in mind that you’ll need 3 inches of space between the frames and the pallet, and 4 inches between each pallet. For example, if you have 40 inches pallets and you want to store two pallets per shelf, you’ll need beams at least 90 inches long. You’ll also need to consider the capacity of the beams you choose. The capacity is determined by the size of the beam face, in addition to the length. The taller the face, the more weight the beam can handle. Conversely, the longer the beam and the shorter the beam face height, the less capacity the beam can safely handle. You can reference this general beam load capacity chart as you do your calculations (capacities are per beam pair):
Beam Length | 3-Inch Beam Height | 4-Inch Beam Height | 5-Inch Beam Height | 6-Inch Beam Height |
---|---|---|---|---|
96 Inches (8 Feet) | 2,000 lbs. | 4,000 lbs. | 6,500 lbs. | 8,000 lbs. |
108 Inches (9 Feet) | 1,500 lbs. | 3,000 lbs. | 5,500 lbs. | 7,500 lbs. |
120 Inches (10 Feet) | 1,200 lbs. | 2,500 lbs. | 4,500 lbs. | 7,000 lbs. |
144 Inches (12 Feet) | 800 lbs. | 1,800 lbs. | 3,000 lbs. | 5,000 lbs. |
This chart is only meant to serve as a basic reference. Beam capacities vary depending on the manufacturer, beam gauge, and various other factors. Consult with a warehouse racking layout professional for specific capacities.
Step 7: Determine the Height
The standard sizes for pallet racking uprights are 8-feet, 10-feet, 12-feet, 16-feet, and 20-feet.To find the right size, you’ll need the your pallet load height, pallet height, number of pallets stored high, beam height, and beam-load clearance (at least 3 inches is recommended – all measurements should be in inches).Once you have this data, you can use this Excel-based calculator to automatically generate the upright height for you. Just click below to download it: Upright Frame Height Calculator Keep in mind you’ll also need to leave 18 to 24 inches of space between the ceiling and the top of your highest pallet, to conform to fire codes. Once you have your height, be sure to take into account the maximum lift height of your forklift. That way, you can ensure you’ll be able to access the materials at whatever height you choose. Once you’ve put all this information together, you’ll have the pallet rack dimensions you’ll need to accommodate your products and materials.
Part 3: Choose Your Warehouse Aisle Width
Once you have your pallet racking dimensions, you’ll want to consider your aisle widths.
That way, you can maximize your existing storage capacity.
Typically, warehouse aisles are broken into the following three categories:
- Wide
- Narrow
- Very Narrow
Let’s go through each one below.
Wide Aisles
Your average sit-down, counterbalance forklift will utilize wide aisles, which are 10.5-feet to 13-feet wide.
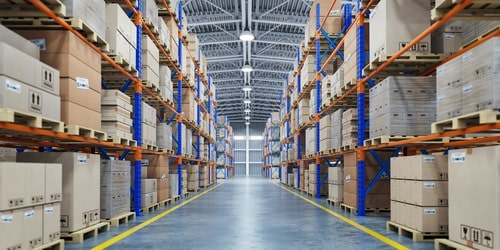
That means you won’t need to invest in specialty equipment.
With wide aisles, however, much of the available space is devoted to the aisles rather than the racking.
So it’s the least optimal aisle width for maximizing storage capacity.
Narrow Aisles (NA)
At 8.5-feet to 10.5-feet wide, narrow aisles allow you to pack more products into your facility.
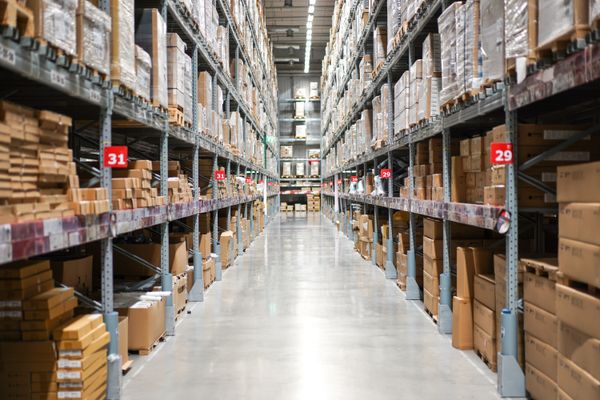
But they require equipment with a tight turn radius to avoid hitting the racking.
Three-wheel forklifts have a tighter turning radius and would be able to work in narrow aisles.
Order pickers and reach trucks are other options for narrow aisle operation.
Overall, users of narrow aisle configurations can realize a 10 to 15% percent gain in storage space over wide aisles.
Very Narrow Aisles (VNA)
At 5-feet to 7-feet wide, very narrow aisles give you the ability to greatly increase capacity without expanding the footprint of your facility.
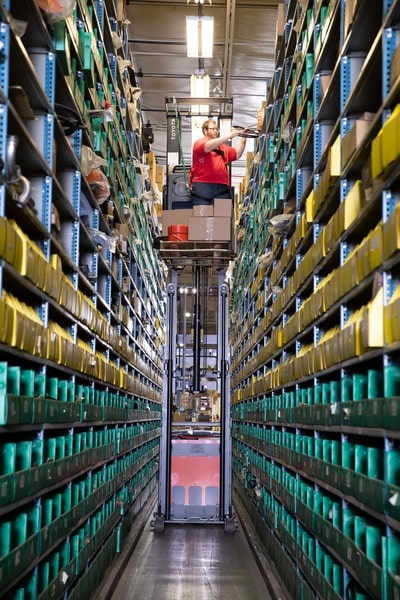
But, you’ll need to take into account the added costs of very narrow aisle forklifts, if you don’t have any in your fleet.
Training your team members on the new equipment will incur additional costs as well.
Overall, very narrow aisles can allow you gains of 25% to 35% over wide aisles.
How to Calculate Your Warehouse Aisle Widths
Choosing your aisle widths is a balancing act.
You want to achieve the optimal storage utilization for your facility, which is between 80 to 85% of your filled floor space.
But you also need to allow enough room to safely and efficiently pick and place products.
Fortunately, you can easily calculate the minimum aisle width for your facility.
Just use this simple equation:
- Basic Right Angle Stack: Minimum amount of space a forklift needs to turn and enter pallets. Found in specification manuals. (Doesn’t include the length of the load)
- Clearance: 12 inches of clearance gives enough space to turn a forklift in the aisle and gives a margin of error for operators without damage to the racking.
- Load Length: Varies depending on circumstances. A standard pallet is 48 inches in length – a good rule of thumb for preliminary calculations. Make sure to use the exact load length for a more accurate representation.
Don’t forget to use the same unit of measurement for all areas of the formula.
Take a look at the example below:
In this example, you end up with a 142-inch minimum aisle width.
Or almost a 12-foot aisle.
This would be a regular aisle width (not narrow or very narrow).
Now that you have all the information needed for your warehouse layout, your racking dimensions, and your aisle widths, let’s talk about the cost of installing pallet racking.
Pallet Rack Prices: What You Can Expect to Pay
When it comes to the cost of warehouse racking, the rule of thumb is the higher the storage density, the higher the cost.
So selective racking – since it offers less density – will cost less than pallet flow racking, for example.
Drawing from TranSystems’ Rules of Thumb: Warehousing & Distribution Guidelines, here are the prices you can expect to pay for warehouse racking:
Selective Pallet Racking
Storage Capacity | Cost |
---|---|
One Pallet Deep | $50 – $75 |
Double Deep | $65 – $90 |
Drive-In Pallet Racking
Storage Capacity | Cost |
---|---|
2 Pallets Deep | $80 – $105 |
3 Pallets Deep | $75 – $105 |
4+ Pallets Deep | $75 – $100 |
Drive-Through Pallet Racking
Storage Capacity | Cost |
---|---|
2 Pallets Deep | $80 – $120 |
3 Pallets Deep | $80 – $115 |
4+ Pallets Deep | $80 – $110 |
Push-Back Racking
Storage Capacity | Cost |
---|---|
2 Pallets Deep | $110 – $140 |
3 Pallets Deep | $130 – $170 |
4 Pallets Deep | $155 – $200 |
5 Pallets Deep | $175 – $220 |
Pallet Flow Racking
Storage Capacity | Cost |
---|---|
2 Pallets Deep | $135 – $260 |
3+ Pallets Deep | $250 – $400 |
Cantilever Racking
Storage Capacity | Cost |
---|---|
8′ Height, Single – Sided Cantilever (four sets of arms) | $465 – $750 |
Double – Sided Cantilever (eight sets of arms) | $610 – $950 |
12′ Height, Single – Sided Cantilever (6 sets of arms) | $550 – $900 |
Double – Sided Cantilever (12 sets of arms) | $950 – $1,400 |
16′ Height, Single – Sided Cantilever (8 sets of arms) | $1,000 – $1,500 |
Double – Sided Cantilever (16 sets of arms) | $1,600 – $2,200 |
Warehouse Racking Safety: Everything You Need to Know
Pallet racking is prone to daily damage and abuse.
And while they’re built to handle heavy loads, that strength has its limits.
Before we get into the nitty-gritty of pallet racking safety, let’s first cover what the Occupational Health and Safety Administration (OSHA) has to say on the topic.
OSHA Warehouse Racking Regulations
Unfortunately, OSHA does give exact guidelines for pallet racking safety.
What they do say on the topic is confined to two standards: 1910.176 and 1910.159.
These standards say that:
- Sufficient aisle space must be given for material handling equipment to pass through
- Aisles should be marked and kept clear of obstructions
- Stored materials must be secure and guarded against movement
- Inventory storage areas must be maintained so they’re free of hazards and pests
- Materials must not be stored within 18 inches of a sprinkler
Beyond that, OSHA’s guidance for pallet racking falls under the “General Duty Clause Section 5(a)(1)“, which states that:
“Each employer shall furnish to each of his employees employment and a place of employment which are free from recognized hazards that are causing or are likely to cause death or serious physical harm to his employees”
While OSHA may not give much in the way of specific pallet racking guidelines, failure to adhere to what they do dictate is a serious matter.
So let’s cover some common OSHA warehouse racking violations.
OSHA Warehouse Racking Layout Violation Fines
Overall, OSHA tends to issue pallet racking violations to employers for:
- Damage: Often from forklift impacts, even seemingly minor damage can affect the safety of pallet racking.
- Unauthorized repairs or modifications: Unless performed by the manufacturer, any type of modification to a pallet racking system can be grounds for an OSHA violation.
- Lack of posted weight capacities: To prevent overloading damage, beams must be marked with the maximum weight capacity limit.
- Improper floor anchoring: To guard against shifting when loading, pallet racking needs to be anchored securely to the floor.
ANSI & Warehouse Racking
Although OSHA doesn’t give much in the way of specific guidelines for warehouse racking layouts, the American National Standards Institute (ANSI) does.
Their guidelines are contained within the “Specification for the Design, Testing and Utilization of Industrial Steel Storage Racks” standard.
And they are the industry-adopted guidelines for pallet racking design and safety.
Please be aware, however, that this document doesn’t apply to all warehouse racking layouts.
Per the abstract:
“The standard applies to industrial pallet racks, movable shelf racks, and stacker racks made of cold-formed or hot-rolled steel structural members. It does not apply to other types of racks, such as drive-in or drive-through racks, cantilever racks, portable racks, etc. or to racks made of material other than steel.”
In it, you’ll find specific information on subjects like:
- Design guidelines for pallet racking parts
- Inspections and maintenance
- Load limits and protection guidelines
For more information, please refer to the free PDF copy linked above.
Note: This PDF was last updated in October 2012.
Please check ANSI’s official website as a newer version may be available.
Pallet Racking Inspections
To ensure your pallet racking is as safe as possible, you must perform regular inspections.
But what counts as “regular”?
Answer: It’s up to the owner’s discretion.
That said, a good rule of thumb is to do them either weekly or monthly, depending on your usage.
These inspections should be performed by someone familiar with the racking systems installed and the installation requirements.
And the results of each inspection should be kept on file in case it’s necessary to reference them in the future.
Overall, there are four items to check while inspecting your pallet racking:
- Plumb and straight
- Rust or corrosion
- Load capacity
- Damage
Let’s go through each one.
Plumb and Straight
Plumb and straight refers to the vertical trueness and degree of twist or bend that a pallet racking upright beam may experience between its centerline at the top and at the floor anchor.
The ANSI pallet racking guidelines we discussed in the last section give the maximum plumb and straight ratio:
The rack height (in inches) divided by 240
For example, if your racking is 12 feet tall (144 inches), the maximum plumb ratio is about 7 inches.
If any uprights exceed that limit, the racking must be unloaded and the problem component repaired or replaced.
Rust or Corrosion
Rust and corrosion can be detrimental to the structural integrity of pallet racking.
It can be an especially big problem if your racking is in a corrosive or moist environment.
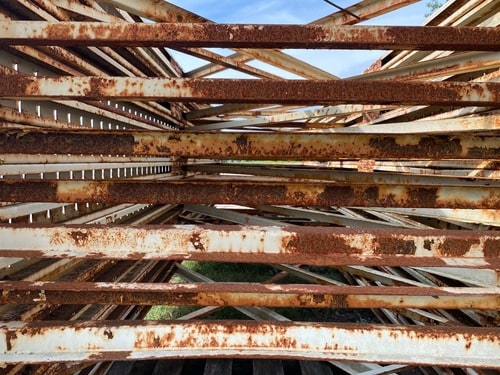
Thus, it’s important to inspect your racking for rust and repair or replace any excessively corroded components.
Load Capacity
Overloading a pallet rack can result in the beams bending and the safety of the racking being compromised.
To help guard against this, each beam in the system should be labeled with the maximum capacity for the shelf.
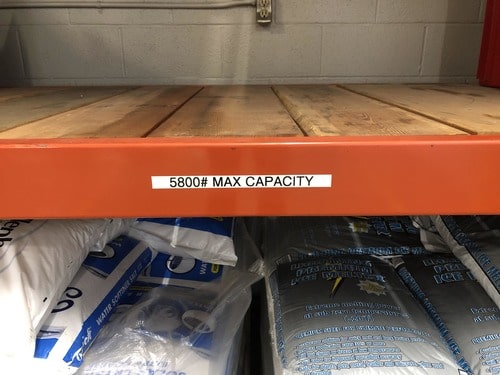
That way, operators will know at a glance whether the racking can handle the load they intend to place on it.
Damage
Indicators of damage can include:
- Beams not engaged with the columns
- Unengaged safety locks
- Missing safety locks
- Damaged uprights
- Damaged bracing
- Deformed beams due to impact
If damage is found, the racking should be unloaded and the problem component either repaired or replaced (according to engineering specifications).
Download our free pallet racking inspection checklist to help you as you perform them.
FAQs About Warehouse Racking Installation
Do I need a building permit to install pallet racking?
Generally, yes.
In many cases, pallet racking is treated like any other building structure.
Thus, local building codes will apply and a permit will be required for installing pallet racking.
What are the pallet rack anchoring standards?
The ANSI guidelines from the previous section state that pallet racks should have anchors on every footplate to resist force.
You can read more about the specifics of that rule on pages 3 and 29-31.
It’s always best to consult an engineer and local building codes to determine exactly what’s required for installing pallet racking in your facility.
How to Prevent Damage to Your Pallet Racking
Once you’ve narrowed down the ideal racking for your warehouse, the last thing you want to see is damage.
Most racking damage is caused by overloading, inadequately engineered systems, or incidents with forklifts.
These issues can cause the center of gravity to shift away from the rack column at the base plate.
This offset causes the column to bend, which creates horizontal force and pushes the column toward the load center.
This cycle – called micro-shifting – continues until the racking structure becomes so unstable that a relatively minor impact can cause a major collapse.
So, what can you do to help prevent damage and possible collapse of your warehouse racking layout?
Let’s go through your options.
Install Protectors
To combat damage to your racking and micro-shifting, you can add additional layers of protection to your racking system.
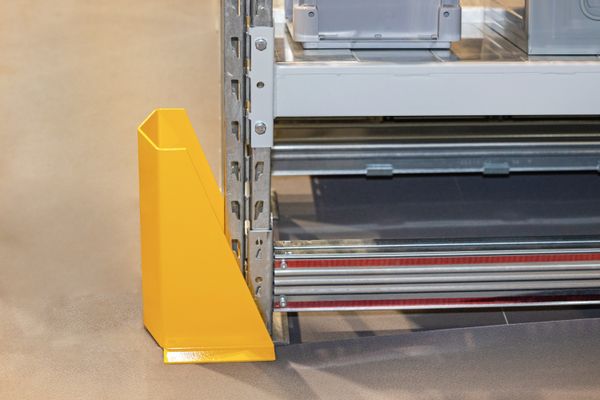
These include:
- Column Protectors to shield the post or column against impacts with a forklift.
- End guard rails to protect the end of each row of racking against forklift damage.
- Off-set/cant legs which are sloped and recessed legs on the lower, front column of the pallet racking frame to provide more clearance for forklifts.
- Rub-rail (for drive-in systems) which are anchored to the floor and act as a bumper for forklifts to protect the racking.
Make Your Racking More Visible
This can include adding lights and installing mirrors near the racking and on the lift trucks.
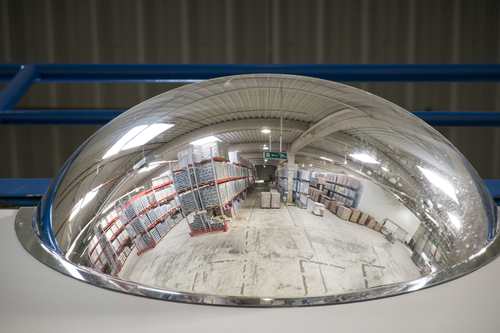
Pay Attention to Load Capacity
You already know that you must install capacity placards on your pallet racking to guard against overloading.
And while pallet racking is designed to carry lots of weight, it’s still good practice to place heavier items on the lower level of your racking if you can.
Improve Your Operator Training
One of the major ways to prevent forklift operators from damaging your racking is training.
Operators should be familiar with the specific lift truck they’ll operate.
Check out Conger’s OSHA-compliant forklift operator safety training course
And they should also understand the procedures for working effectively with and around the kind of pallet racking you use.
Lower Your Speed Limits
If impacts are an issue in your facility, consider lowering the speed limit for your material handling equipment.
Posting the speed limit where operators will see it can help reduce impact damage.
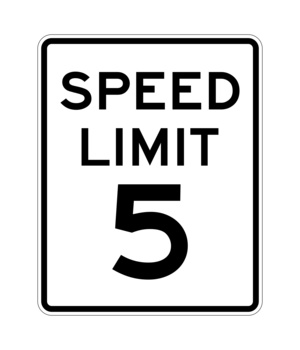
But if posted speed limits aren’t working, consider setting the speed control on your lift truck – if it’s equipped – to electronically limit the maximum travel speed.
Your local forklift dealership should be able to help you do this.
Conclusion
There you have it: the complete guide to warehouse racking.
Now we’d like to turn it over to you.
What kind of warehouse racking does your facility use?
Or are you still deciding what the best option is for a new installation?