Forklifts are essential tools in warehouses and other industrial settings and understanding the key parts of a forklift can help improve safety, maintenance, and overall performance.
In this guide, we’ll walk you through the major components of a counterbalance forklift, explain their functions, and highlight important safety features.
Whether you’re new to forklifts or need a refresher, this article will break down everything you need to know about the different parts of a forklift.
Let’s dive in!
What Are the Three Major Parts of a Forklift?
Answer: The chassis, the mast, and the overhead guard.
Additionally, forklifts have numerous safety devices distributed throughout the truck.
But within these groups, there’s more to the story.
So what follows in this article is a breakdown of each group.
The Chassis: What’s All Part of It?
The chassis is comprised of 4 major components:
- The counterweight
- The engine or battery compartment
- The operator compartment
- The wheels and tires
Let’s go through each one.
The Counterweight
A forklift counterweight is a weight mounted on the rear of a forklift.
What does the counterweight do on a forklift?
Answer: It counteracts the weight on the forks and provides for the proper weight distribution of the truck.
If you think of a forklift as a teeter totter, this may make more sense.
The front wheels act as the fulcrum – or balancing point.
So any weight ahead of the front wheels needs to be balanced by weight behind the wheels.
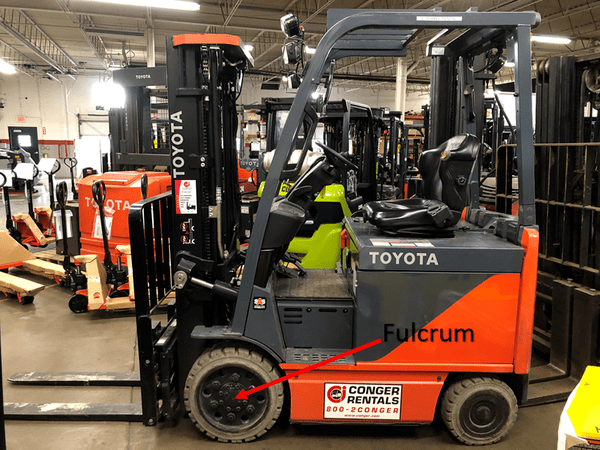
Without that counterbalance, a loaded forklift would become too heavy on the front.
And this would cause the lift truck to tip forward – rendering it useless and potentially causing injury.
What Are the Main Types of Forklift Counterweights?
There are two main types of forklift counterweights:
Bulk-Type
This is the most common type of counterweight you’ll see on a forklift.
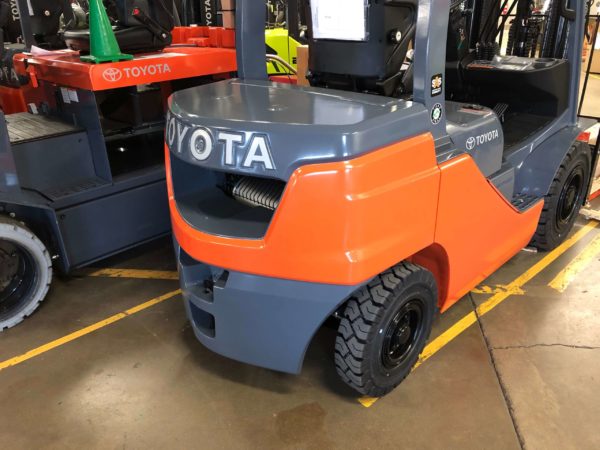
Bulk-type counterweights are designed with a hollow body that’s typically lead-filled.
They can also consist of a single metal casting or a hollow metal container with a mix of concrete and metal.
Stack-Type
Stack counterweights are usually used on high-capacity forklifts.
These have metal plates or cast metal housings/steel canisters designed to stack onto a base plate.
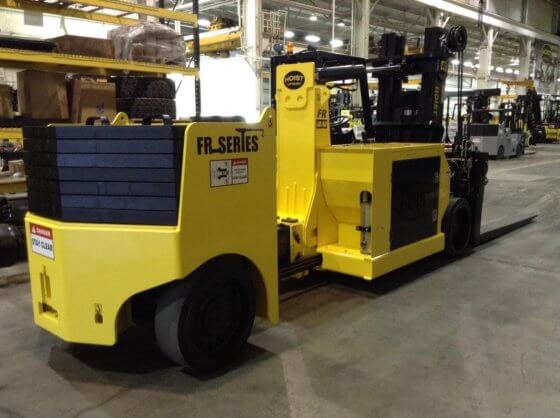
Removing or stacking these plates enables the lift to handle more weight.
Lift trucks with stack-type counterweights can have as many as six plates stacked, each at 2.5 tons.
Electric Forklifts and Counterweights
Electric sit-down forklifts have smaller counterweights than internal combustion (IC) forklifts of the same lifting capacity.
Why?
Because the battery on an electric forklift helps provide much of the counterweight.
After all, forklift batteries weigh several tons at a minimum
Thus, a full-sized counterweight isn’t necessary for electric forklifts.
The Engine/Battery Compartment
The power source for a forklift is housed in the engine or battery compartment, depending on the type of forklift.
For sit-down internal combustion forklifts, the engine compartment is located directly beneath the operator’s seat.
Parts of a internal combustion forklifts engine include the:
- Engine
- Transmission
- Fuel system (for gas, diesel, or propane-powered forklifts)
- Radiator and cooling system
- Air intake
- Hydraulic valve, pump, and tank
- Electrical fuse box
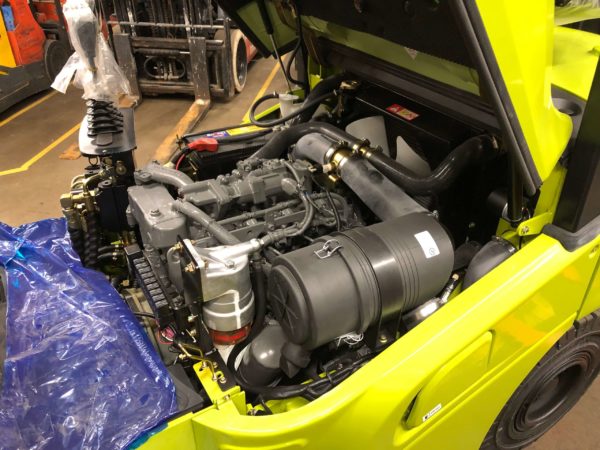
In electric forklifts, the battery compartment is also located under the operator’s seat. The battery serves as the primary power source, driving all of the forklift’s operations.
Electric forklifts are powered by large industrial batteries that need regular charging.
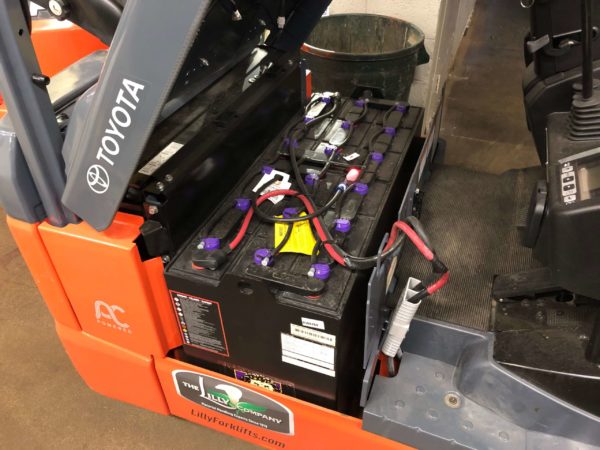
Forklifts can be powered by different sources, including propane, diesel, gas, or electric. Propane-powered forklifts often feature externally mounted tanks for easy access and replacement. Electric forklifts are known for their quiet operation and are popular in indoor environments.
Understanding the location and function of the power supply is crucial for safe operation and regular maintenance of both internal combustion and electric forklifts.
Hydraulic System
Unlike internal combustion forklifts, electric forklifts do not have components like a transmission, fuel system, or cooling system.
However, they rely heavily on their hydraulic system to operate the mast and forks.
The hydraulic system consists of hydraulic pistons, cylinders, and fluid that control the lifting, tilting, and lowering of loads.
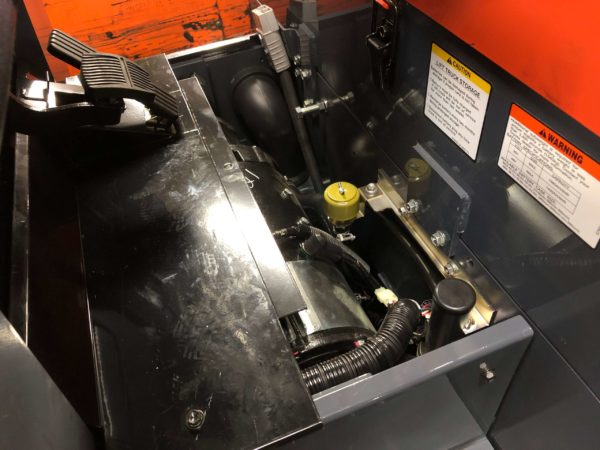
On a Toyota electric forklift, the hydraulic system is located beneath the floorboard, where the operator’s feet rest.
This system includes the hydraulic lift cylinders and tilt cylinders, which connect to the truck frame and mast.
The hydraulic lift raises and lowers the forks, while the tilt cylinders allow the mast to tilt forward or backward for safe handling of loads.
Operator Compartment
The operator compartment, also known as the operator cab, is where the forklift operator sits or stands to control the vehicle.
This space contains essential controls and safety features that enable efficient and safe forklift operation.
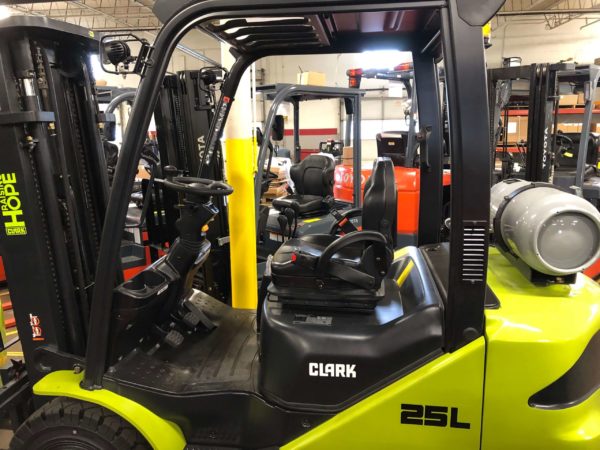
Common Components in the Operator Compartment:
Steering Wheel
The steering wheel is used to maneuver the forklift and often includes a horn for safety. It’s a critical component for directing the forklift’s movement.
Seat and Seatbelt
Forklifts are equipped with seats and, in newer models, mandatory seatbelts to ensure operator safety during operation.
Pedals
The operator compartment contains various pedals, including the accelerator, service brake, parking brake, and inching pedal. These pedals control the movement, stopping, and fine-tuning of the forklift’s positioning.

Levers
Forklifts typically have three main hydraulic control levers:
- Lift lever to raise and lower the forks.
- Tilt lever to adjust the mast forward or backward for load stability.
- Auxiliary lever for attachments, such as side shifters, that provide additional functionality.
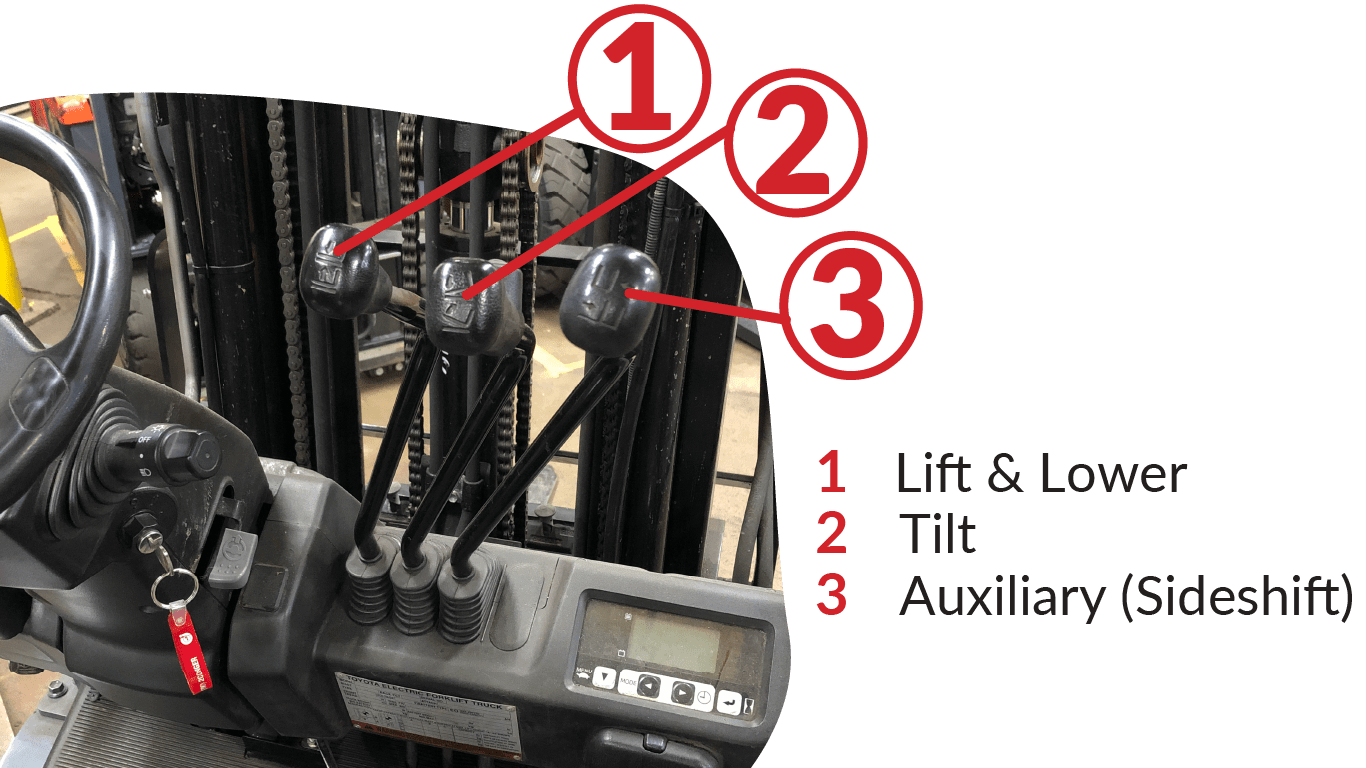
Some forklifts may have more levers to control other attachments.
Gauges
The forklift’s instrument panel includes various gauges and indicators such as an hour meter, engine temperature gauge, speedometer, and warning indicators.
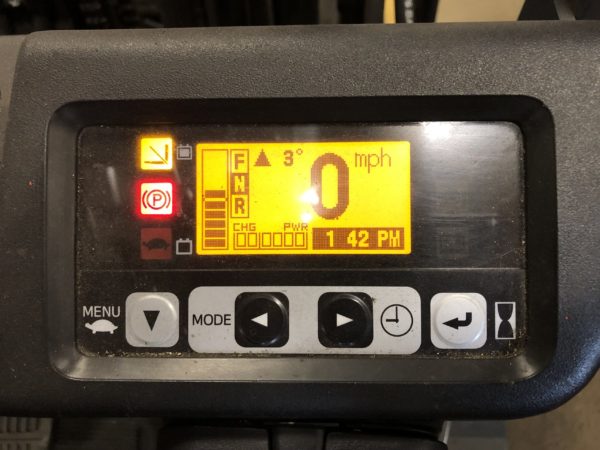
Just like in a car, these gauges monitor the forklift’s performance and alert the operator to any issues.
Data Plate
Also called a capacity plate or nameplate, the data plate provides crucial information about the forklift’s design and capabilities, such as:
- Forklift weight
- Fuel or battery type
- Mast type
- Attachments
- Load capacity
- Tire size
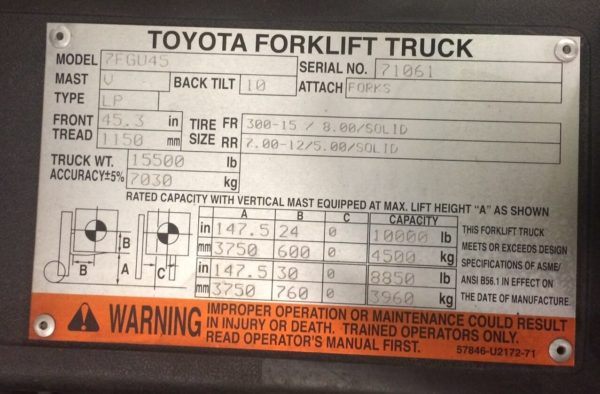
Operators must understand the data plate before operating the forklift to ensure they are aware of its capacity and limitations.
Safety Features:
The operator compartment is equipped with several safety devices to protect the operator.
The overhead guard, for example, shields the operator from falling objects.
Additionally, some forklifts include advanced safety systems like seat sensors that prevent operation unless the operator is seated and belted.
The Wheels and Tires
Forklift wheels and tires are different from those in road vehicles.
For one, there are various types of tires available.
For another, forklifts steer in the opposite way than cars do.
And finally, forklifts do not have any suspension connected to the wheels.
Let’s cover forklift wheels and tires in more detail.
Forklift Wheels
Forklifts have two types of wheels: Drive wheels and steer wheels.
Drive Wheels
Drive wheels are located on the front axle of the forklift and are what the engine or electric motor supplies power to in order to move the lift truck.
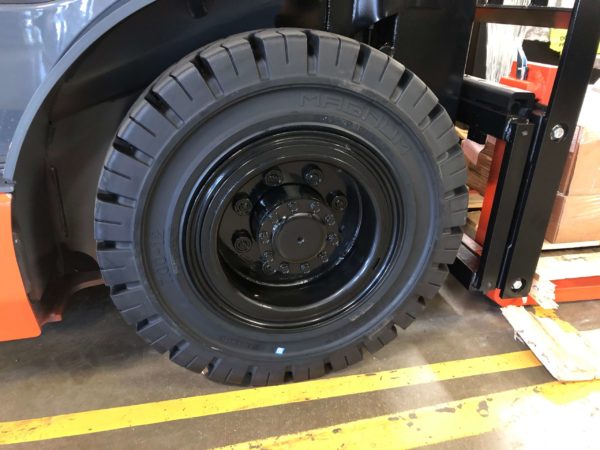
These wheels do not steer left and right.
Instead, they support most of the load from the mast in a fixed position.
Steer Wheels
These are located on the rear axle of the forklift.
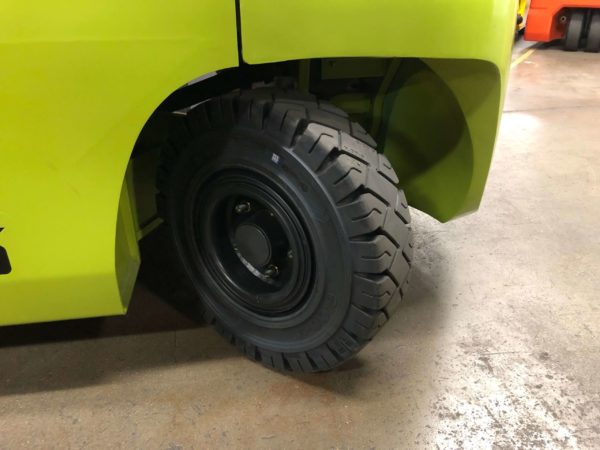
They allow the lift truck to turn, and also act as support for the counterweight.
Why Is Forklift Steering Backwards?
Answer: Because the front drive wheels support the weight of the load.
If the drive tires could turn, the forklift would become unstable and potentially tip over.
So instead, forklifts are designed to steer from the rear to keep the truck steady under a load.
Forklift Tires
Forklifts have different types of tires depending on the type of forklift and application.
The main types of forklift tires are:
Pneumatic
These tires are filled with air, just like car tires.
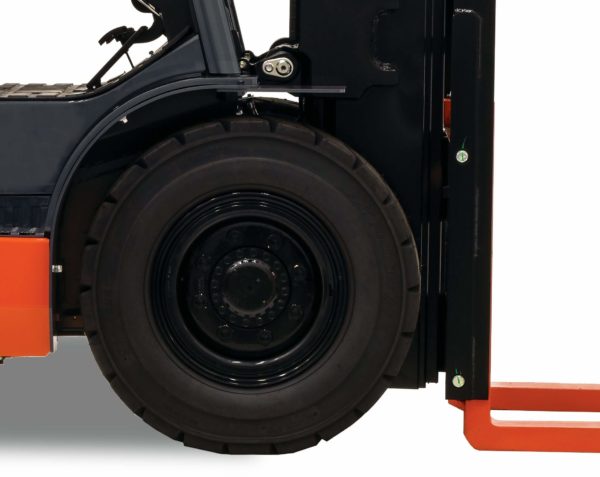
Overall, they have better traction and stability on uneven terrain.
But they are prone to punctures from nails and metal debris.
Solid Pneumatic
Solid pneumatic tires are like air pneumatic tires.
But instead of being filled with air, they’re typically filled with foam.
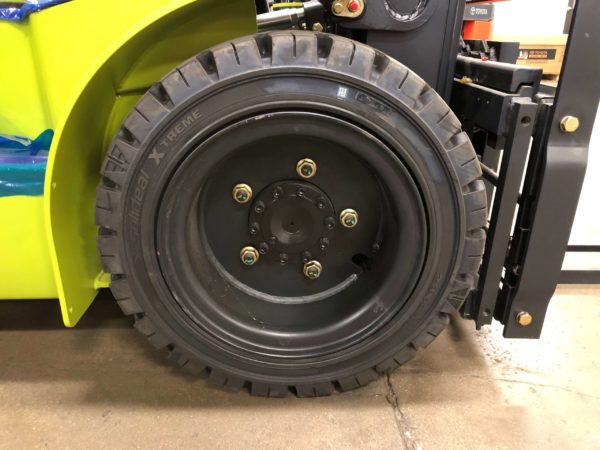
That also makes them more expensive than air-filled pneumatic tires.
Solid pneumatics are best for outdoor areas with a lot of debris that can puncture air-filled tires.
They’re typically used in lumber yards, scrap yards, and construction sites.
Cushion
Cushion tires (also called press-on tires) are made of solid rubber molded to a steel band.
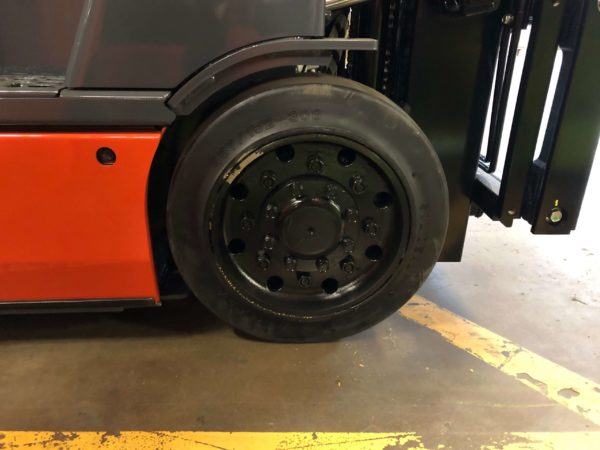
They’re ideal for indoor use on smooth driving surfaces or light outdoor use.
Many forklift users choose to outfit their lifts with non-marking cushion tires.
The advantage of these is that they won’t scuff up the floor as regular black cushion tires will.
The Mast: What’s All Part of It?
If you’re wondering “What is the front part of a forklift called?” the answer is the mast.
A forklift mast, also called upright, is the part of the forklift that lifts, positions, and lowers the loads that forklifts handle.
Types of Forklift Masts
There are 4 types of forklift masts:
Single-Stage Mast
A single-stage mast – also called a “Simplex” forklift mast – has one channel and, therefore, a limited lifting height.
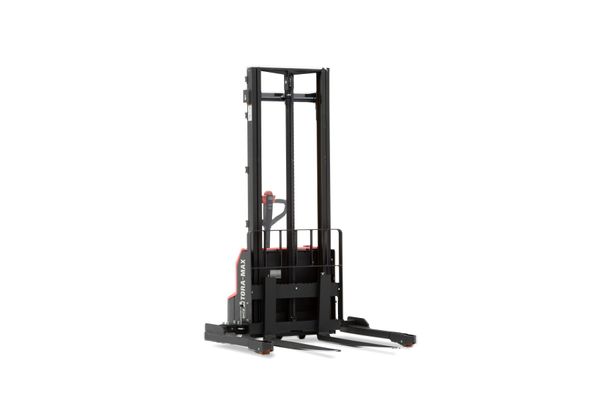
They have zero free lift capability, meaning as the forks rise, the top of the mast also rises.
So, these types of masts are best for outdoor environments or applications where overhead clearance doesn’t matter.
Two-Stage Mast
A two-stage mast – or “Double” or “Duplex” mast – has two channels or sections either with or without full free lift capabilities.
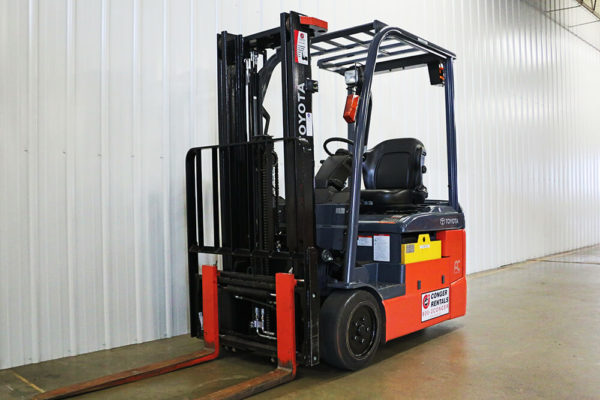
A 2-stage mast is best for jobs that don’t need to lift very high.
An example is loading and unloading flatbed semi-trailers.
Three-Stage Mast
Also called a “Triplex,” “Triple,” or “Triple Stage Upright (TSU),” this is the most common type of mast.
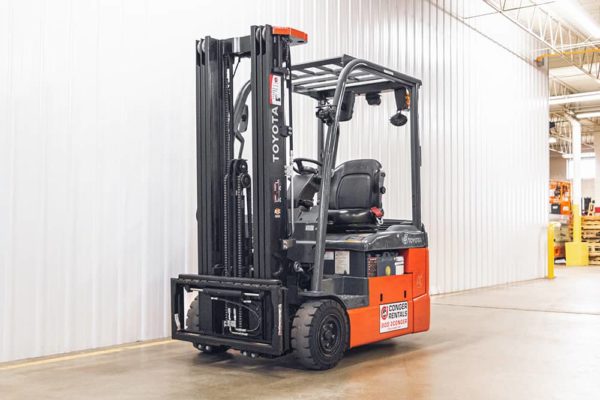
A 3-stage mast has three sections.
These sections extend the carriage and forks to the maximum lift height with two sliding rails on the sides and a single stationary rail.
It enables loading and unloading at greater heights than single- or two-stage masts.
Quad Mast
This mast uses four sets of rails with added chains to give four stages of lifting with full free lift.
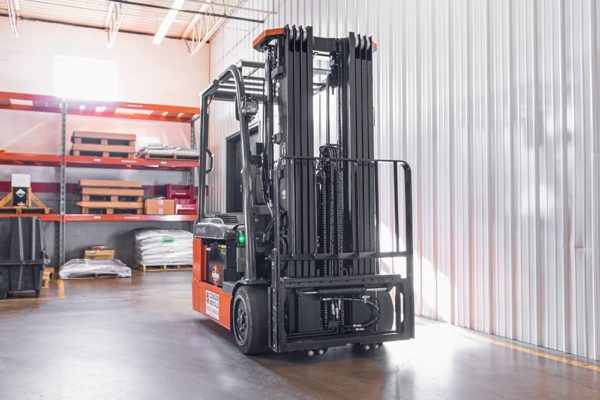
It provides the highest reach and is commonly used in very high stacking in specialized warehousing.
What Are the Main Forklift Mast Parts?
The parts of a forklift mast include:
- Rails
- Cylinders
- Chains
- Carriage
Let’s go through each part.
Rails
The rails are the “frame” of the mast.
They allow the mast to extend up to its maximum fork height (MFH) or down to its collapsed or lowered height.
Lift Cylinders
Also called hydraulic cylinders, lift cylinders harness hydraulic power to raise or lower the mast and load.
There are 2 types of lift cylinders:
- Free lift
- Outboard
Free lift cylinders are mounted in the center of the mast and allow the carriage to rise without extending the rails through the top of the mast.
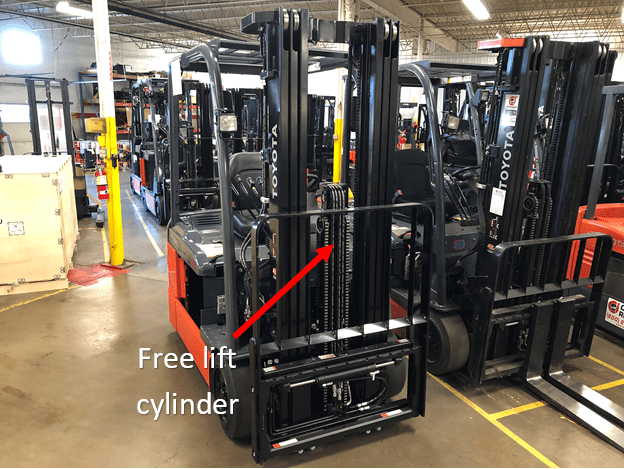
The outboard cylinders are located in the rear of the mast and push the nested rails upward.
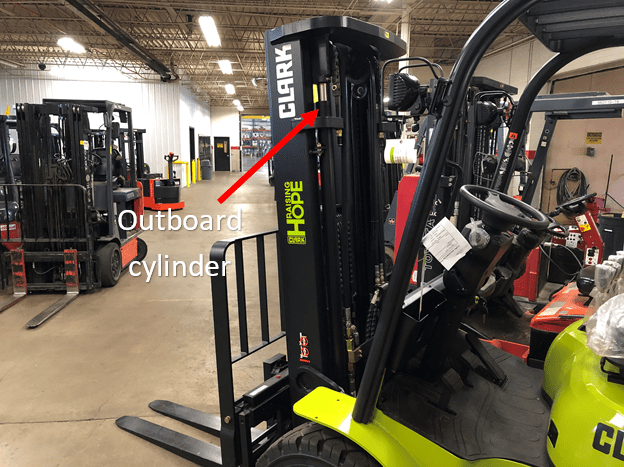
Tilt Cylinders
These control the forward and backward movement of the mast.
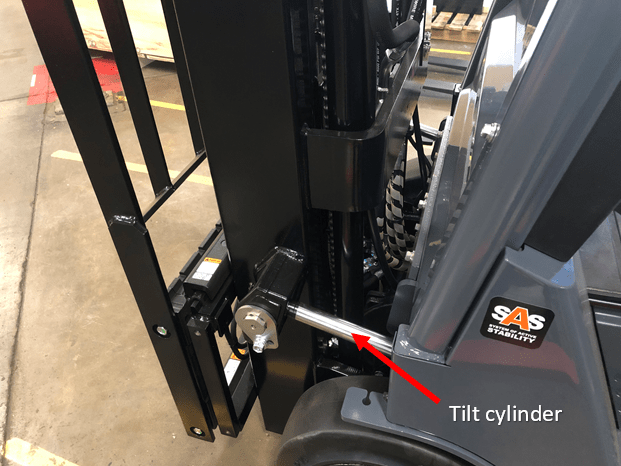
They’re double-acting hydraulic cylinders, meaning they can both push and pull.
Lift Chains
Forklift mast chains attach the carriage to the hydraulic cylinders.
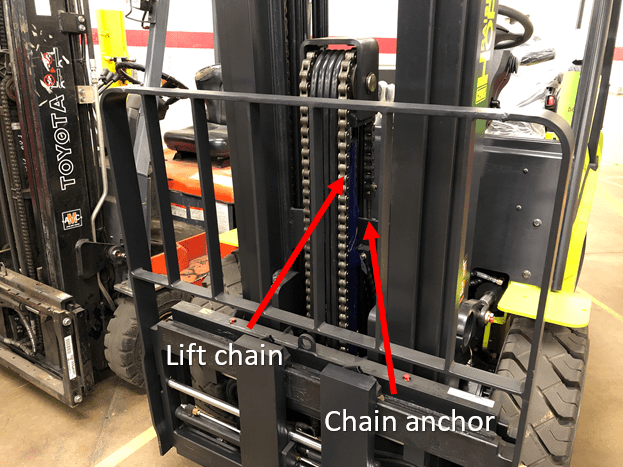
They function in combination with lift cylinders and rails to raise and lower the carriage.
Carriage
The carriage is the platform that supports and moves the forklift’s forks and attachments, such as the load backrest.
Mounted onto the mast rails, it moves vertically to lift and lower loads.
The carriage has a mounting rail for various attachments and makes direct contact with the load.
The load backrest, bolted to the carriage, helps prevent the load from shifting backward off the forks.
Carriage Class Sizes
Carriages come in different sizes, each designed to handle specific weight capacities.
Below are the five carriage classes and their respective lifting capacities:
Class | Carriage Height | Lifting Capacity |
---|---|---|
I | 13″ | <2,200 lbs. |
II | 16″ | 2,200 lbs. – 5,500 lbs. |
III | 20″ | 5,500 lbs. – 10,998 lbs. |
IV | 25″ | 11,000 lbs. – 17,600 lbs. |
V | 28.66″ | 17,602 lbs. – 24,198 lbs. |
Attachments
Attachments mount to the carriage and are what actually handle the loads.
Common forklift attachments include:
Forks
Forks are the horizontal prongs used to lift and carry loads.
They hook onto the carriage and come in various lengths to accommodate different applications.
Common fork sizes include:
- 42″
- 48″
- 54″
- 60″
- 72″
- 96″
Forks are designed to make direct contact with the load, supporting it from the bottom.
The most common type of forklift forks is the Standard ITA Fork, but there are many fork types available, depending on the specific job requirements.
What Are Forklift Tines?
“Tines” is another term for forklift forks. These prongs slide under the load, allowing the forklift to lift and move it safely.
No matter the name—tines, forks, or blades—they all serve the same purpose. Forklift forks are crucial for ensuring stable load support and efficient transport of goods.
Sideshifters
A sideshifter hooks onto the carriage and forks hook onto the sideshifter.
With this arrangement, operators can move a load from side to side.
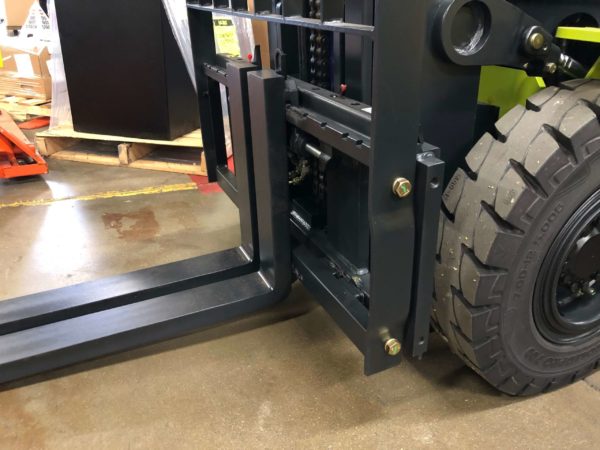
In doing so, the operator can make minor adjustments to the load alignment without maneuvering the entire forklift.
Fork Positioners
Fork positioners are typically sideshifters with extra hydraulics that allow side-to-side positioning of the forks.
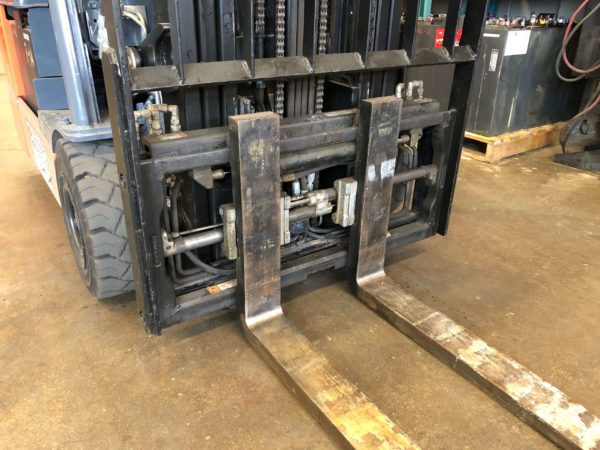
They are essential when the load’s width constantly changes since they allow the operator to quickly align the forks with the pallet channels.
Paper Roll Clamps
These attachments are designed to handle cylindrical paper rolls.
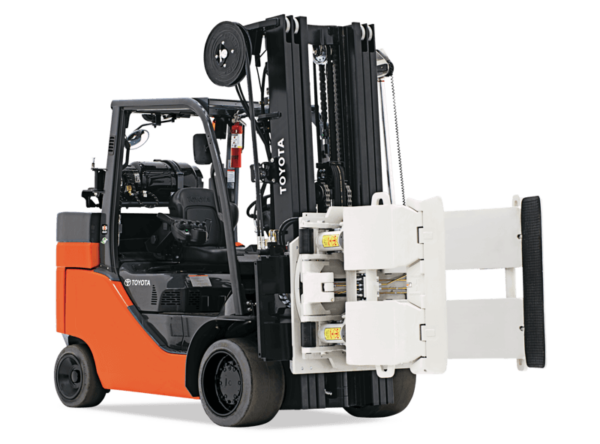
As you can imagine, they’re commonly used in the paper and printing industries.
Multiple Pallet Handlers
Another common name for this style of attachment is the “single-double.”
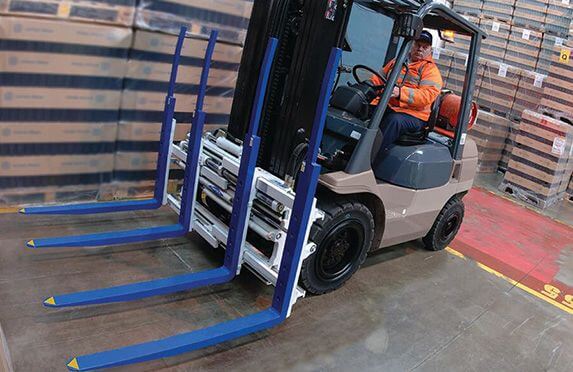
These allow operators to handle more than one pallet by hydraulically spreading multiple sets of forklifts.
Then, the operator can carry multiple pallets at the same time.
Slip Sheeters
Also called a “push/pull” attachment, these are designed to handle non-palletized goods.
To do so, the attachment grabs onto the “slip sheet” under the load.
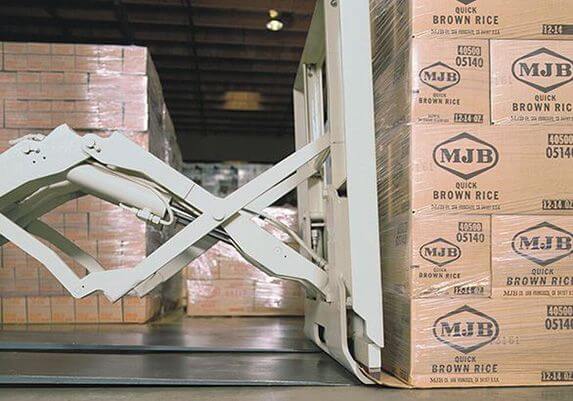
Then, the attachment retracts and pulls the load onto the forks beneath.
These are commonly used in sensitive industries like food and pharmaceuticals where using wood pallets could contaminate the products.
The Overhead Guard: What’s All Part of It?
The overhead guard is a safety feature designed to protect the operator from falling objects while within the confines of the operator compartment.
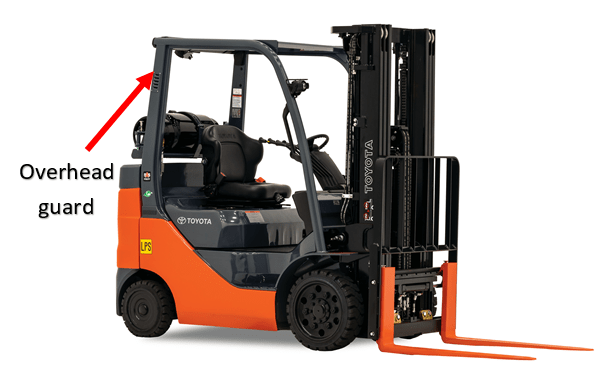
Since the 1960s or so, overhead guards have been standard equipment on forklifts.
And in fact, they are required by OSHA, which states that:
“An overhead guard shall be used as protection against the impact of small falling objects such as boxes, debris, small packages, bagged material, etc. But, they’re not able to withstand the impact of a falling capacity load.”
Safety Equipment: What’s All Part of It?
In past years, forklifts had practically zero safety features.
Today, there are many different options for keeping operators, supervisors, and pedestrians safe.
These include:
Seatbelts
Like car seat belts, forklift seat belts save lives as they restrain the driver and prevent them from being catapulted out of the compartment in case of a tip-over.
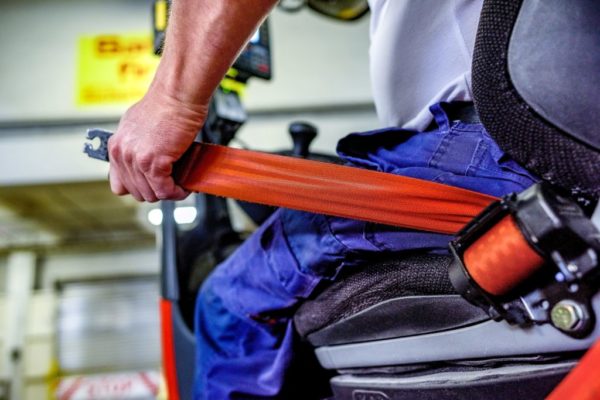
Headlights
These are commonly found on forklifts working in dark areas, like semi-trailers, to improve visibility.
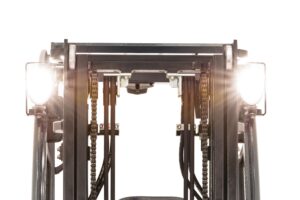
Warning Lights
Warning lights can take many forms.
One popular type is blue lights.
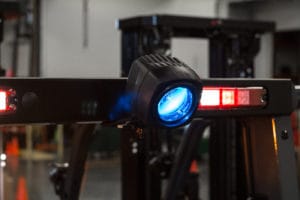
These are used to alert pedestrians and warehouse workers that a forklift is approaching.
Red-Zone lights are another type of warning light.
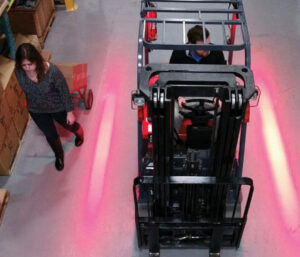
They are used to alert pedestrians/warehouse workers of how close they can get to the forklift.
Mirrors
Mirrors are mounted on the left and right pillars of the overhead guard to allow the operator to see behind the fork truck.
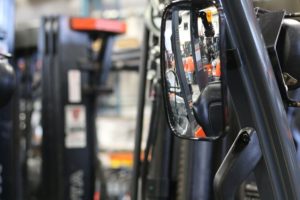
Not all forklifts have these, nor are they required.
Brake Lights and Turn Signals
These for extra signaling, just like on a car or truck.
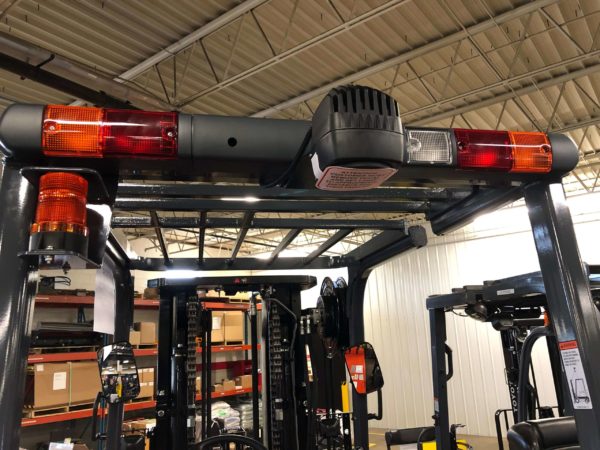
But like mirrors, not all lift trucks have them.
Strobe Lights
Strobe lights are typically mounted on the rear of the overhead guard where everyone can see them.
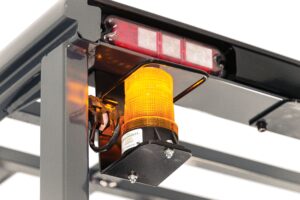
They serve as a universal sign that workers should be alert.
Travel Alarm
These provide audible warnings either when the forklift is in motion or just when the forklift is backing up.
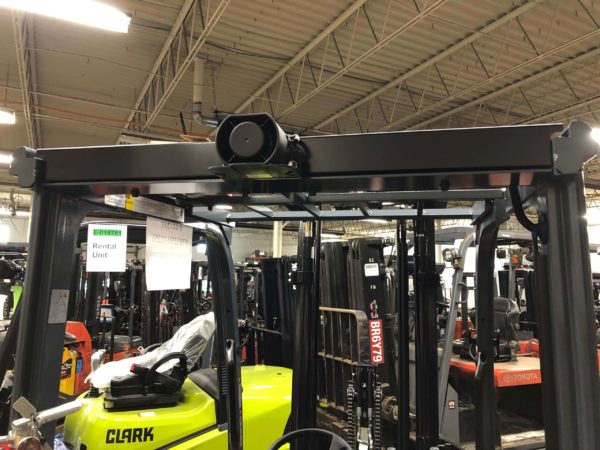
Forklift Horn
Forklifts must be equipped with horns.
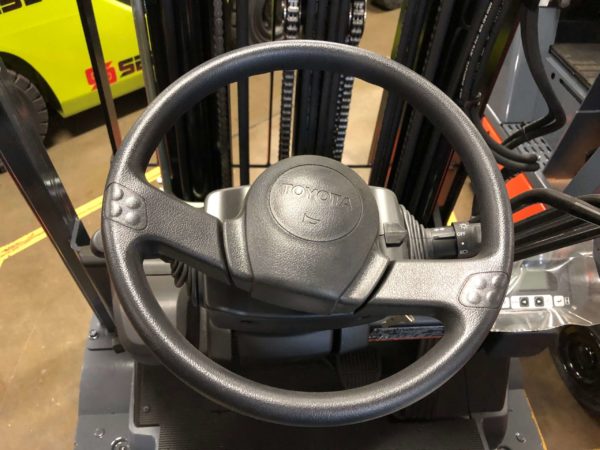
They provide a warning when crossing thresholds that may have pedestrians nearby.
Conclusion
Now that you’ve explored the main parts of a forklift and their functions, you have a solid foundation for understanding how these machines operate. From the chassis and mast to the safety equipment, each component plays a critical role in the forklift’s performance and safety. Whether you’re maintaining a forklift, operating one, or just learning more, knowing these details will help you use forklifts more efficiently and safely.