Forklift accidents can have serious consequences, from property damage to life-altering injuries.
That’s why understanding the risks and taking proactive steps toward safety is so important.
In this post, you will discover:
- The top 10 most common forklift accidents (in no particular order)
- How employers and operators alike can reduce lift truck accidents in the workplace
- Eye-opening accident and injury statistics
Let’s dive in.
Here are key statistics that highlight the prevalence and risks of forklift accidents.
Forklift Rollovers
Rollovers are the most common type of fatal forklift accident.
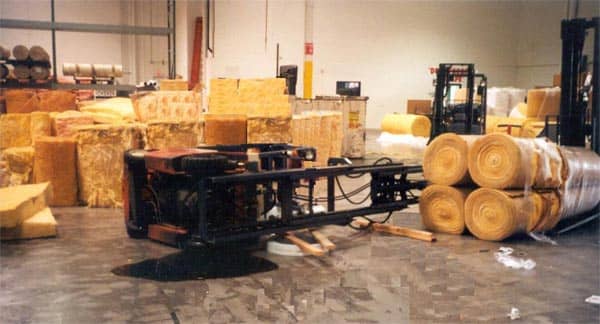
In the event of a tip-over, operators of sit-down forklifts should stay in their seats, brace themselves, and lean away from the point of impact.
Operators of stand-up forklifts should step back and out of the operator compartment and away from the truck.
And as always, wear your seat belt!
Main Causes of Rollovers
- Turning too quickly
- Overweight, uneven, or unbalanced loads
- Abrupt mast movement
- Turning on an incline
- Driving with the load elevated
- Driving on uneven surfaces
How to Prevent Rollovers
Follow set speed limits: Adhere to OSHA-mandated speed limits and adjust vehicle speeds to prevent rollovers. Fortunately, numerous forklift manufacturers enable employers to change the speed limit on their vehicles, helping prevent speeding incidents.
Slow down when rounding corners: When turning, the center of gravity of the lift truck can move outside the zone of stability, increasing the risk of tipping over.
Toyota’s System of Active Stability (SAS) enhances stability by automatically adjusting the rear axle when instability is detected, helping to keep the truck upright:
Don’t exceed your lift’s capacity. Check the truck’s data tag if you’re unsure what weight it can handle.
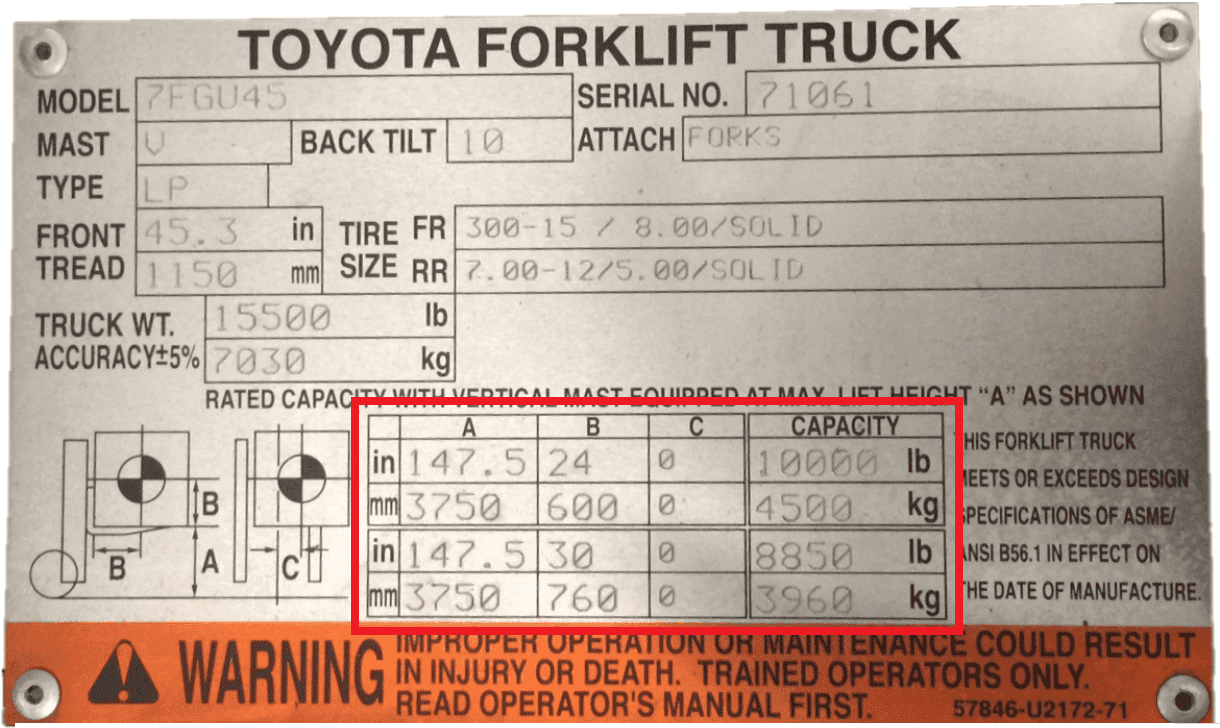
Use care when tilting a raised mast. Tilting too abruptly can cause the forklift to tip forward and over. And only raise or lower the load when the forklift is not moving.
Toyota’s Active Mast Function Control System limits forward and rear tilt speed when instability is detected, helping to prevent tip-overs:
Never turn on an incline. Descend the incline, then turn.
Keep the load as low to the ground as possible. Lift trucks are more stable with a load on the forks. However, this is only true if the load is near the ground. Elevated loads tend to make the forklift load balance unstable.
Only operate on smooth, even surfaces. Potholes and other roadway imperfections can cause the truck to tip over.
Pedestrian Impacts
Forklifts often operate in close quarters with workers on foot.
So it’s no wonder that one of the most common types of lift truck accidents involves pedestrians.
Main Causes of Pedestrian Impacts
- Operator inattention, including fatigue, distracted driving, and carelessness
- Lack of warning signs and signals
How to Prevent Pedestrian Impacts
Allow operators more breaks. Long driving shifts without regular breaks can have serious safety consequences. OSHA reports that workers who work 12-hour shifts are 37% more at risk of injury.
Use care when operating near pedestrians who are next to a fixed object. Lack of operator awareness can easily lead to pinning pedestrians between the truck and the object.
“Trucks shall not be driven up to anyone standing in front of a bench or other fixed object.” – OSHA 1910.178(m)(1)
Put down floor tape. Use this to mark pedestrian and forklift traffic to ensure workers know where to travel safely.
There are several different measures that you can install to help improve pedestrian safety. These measures include:
- Barriers: Physical structures can separate forklift traffic from pedestrian walkways, preventing injury when impacts do occur.
- Wall-mounted mirrors: With mirrors, operators can see around blind spots before proceeding.
- Warning lights on lift trucks: Forklift warning lights, such as blue lights, increase pedestrian visibility so they know when a forklift is approaching.
- Travel and/or backup alarms on forklifts: These add-ons are effective in noisy environments and can alert pedestrians and other operators to the presence of a lift truck in the area.
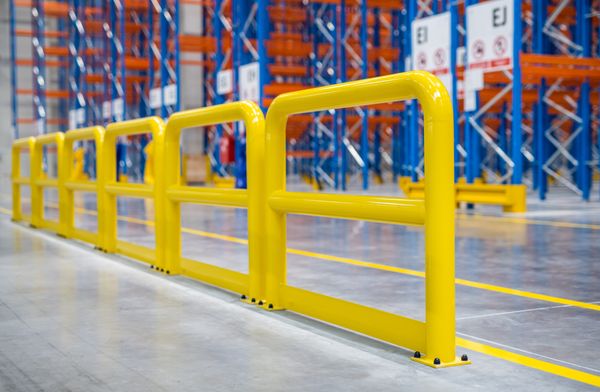
Consider implementing these measures to enhance workplace safety. Speak with your local material handling dealer to get a quote. If have operations in the Green Bay, Neenah, Wausau, Richfield, and Madison areas, Conger has dealerships ready to help improve your material handling vehicles.
Lack of Operator Training
OSHA mandates that every operator be trained and certified before using a forklift. Unfortunately, this doesn’t always happen.
Accidents are more likely when operators are unfamiliar with the proper safety policies and procedures for operating forklift trucks.
Just take a look at the video below to see how training could’ve helped avoid some serious forklift accidents:
Luckily, inadequate training is easy to overcome. Doing so can decrease the likelihood of injuries while using forklifts.
Main Causes of Inadequate Operator Training
Unknown need. Supervisors and managers may be unaware of the laws on forklift operator training.
Cutting corners. When companies are on a tight schedule and short on time or budget, there can be a temptation to skip training to keep things moving.
How to Prevent Inadequate Operator Training
Sign up for OSHA-compliant operator training. The logic is straightforward: Better training leads to fewer mistakes and accidents. OSHA reports that proper training can help reduce forklift accidents by up to 70%!
Are you interested in having forklift training? Check out Conger’s page on OSHA-compliant forklift operator safety training courses for more information.
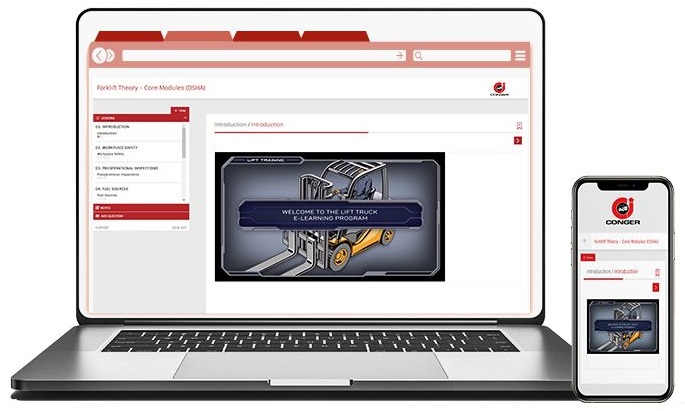
Focus on the return on investment (ROI). Instead of looking at the time and cost of training, companies should see how much they can save. One survey of chief financial officers (CFOs) found that businesses can earn back $2 for every $1 spent on injury prevention!
Falling Loads
Forklift operators do not just carry simple loads like boxes and pallets.
Much of the job involves lifting and transporting raw materials, small items, and other loads that can fall if not properly secured.
Falling loads are a hazard to pedestrians and operators alike.
Preventing injuries and fatalities requires the assurance that loads remain securely in place on the forks.
Main Causes of Falling Loads
- Improper load creation: Off-center, damaged, or loose loads
- Moving, lifting, or tilting the mast too fast
- No load backrest
- Bent forks
How to Prevent Falling Loads
Don’t carry loose or damaged merchandise. Take the time to properly secure loads before transporting. Use banding and/or shrink-wrap to ensure all materials stay on the pallet or forks.
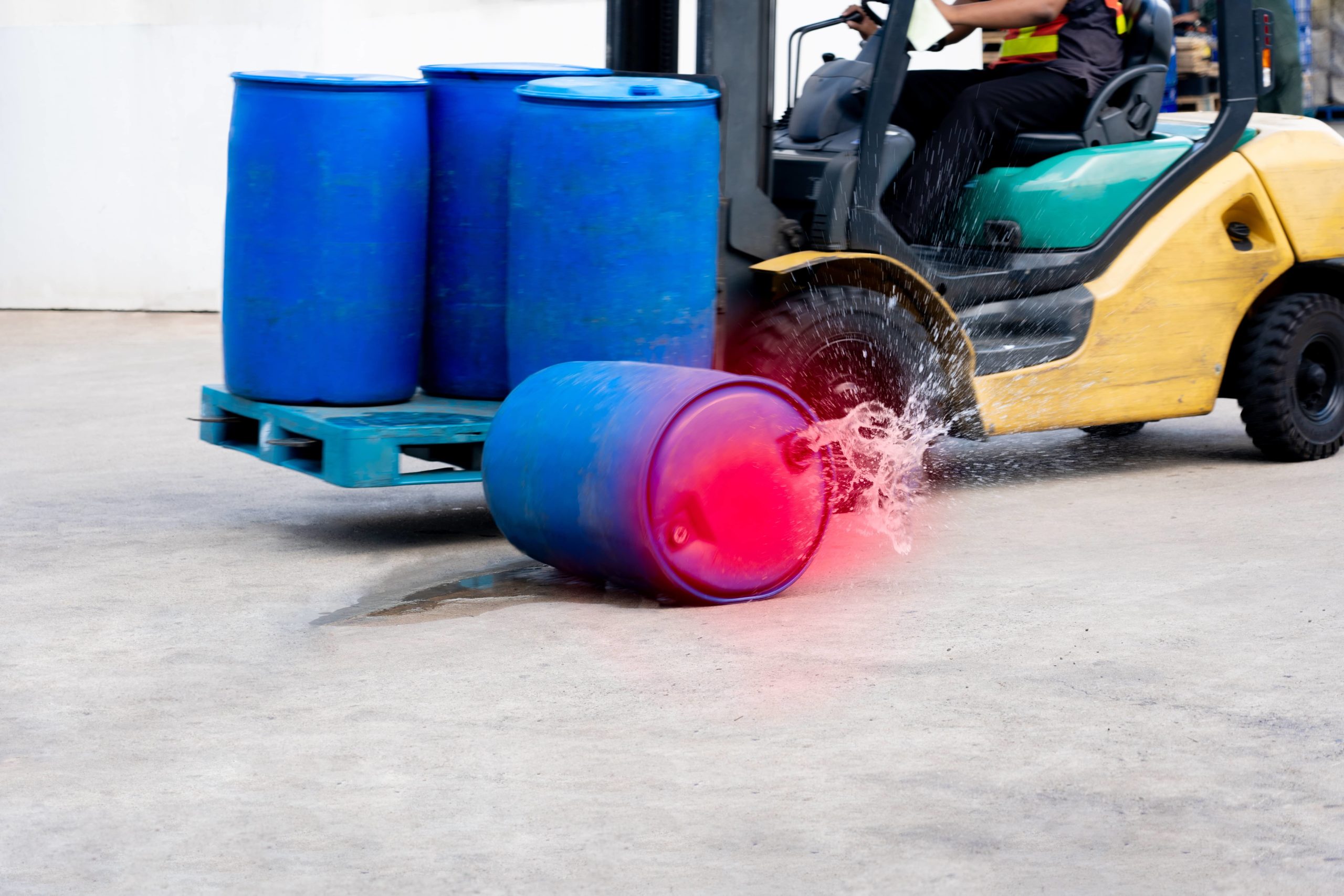
Center the load. If the product cannot be centered, place the heaviest part closest to the front wheels of the forklift against the carriage.
Use care when tilting the mast. Jerky movements, especially when retrieving items from racking, can cause materials to come loose and fall.
Use a load backrest. A backrest will help prevent items from falling backward into the mast or the operator’s compartment.
Conduct a pre-trip inspection before every shift to ensure the forks are even and overhead guards are intact.
Remember that overhead guards are not to absorb the full impact of a load, but they can guard against small falling objects.
Download Our Free Daily Forklift Inspection Checklist
Print and reuse these inspection checklists as often as you need to. Choose whichever format you’d prefer below and click to download.
Truck Falling Off a Dock or Trailer
One of the most dangerous activities for forklifts is crossing thresholds.
Whether that is moving between areas of a warehouse or into and out of semi-trailers, operators must be vigilant in making sure it’s safe to proceed.
Main Cause of Falls to Lower Levels
- Trucks or trailers rolling away
- Slippery floors
- Worn or damaged truck or trailer floors
- Improper or no dock plate
How to Prevent Falls to Lower Levels
Chock truck/trailer wheels before entering. The weight and forward movement of a forklift entering a trailer or truck can cause it to lurch forward if the wheels aren’t secure.
“The brakes of highway trucks shall be set and wheel chocks placed under the rear wheels to prevent the trucks from rolling while they are boarded with powered industrial trucks.” – OSHA 1910.178(k)(1)
Slow down when approaching the dock. Reduce speed and inspect for potential hazards like liquids or debris and clean them up before proceeding.
Inspect the floor of the truck or trailer before driving on it. Missing boards, uneven floors, or debris can lead to a fall.
“…The flooring of trucks, trailers, and railroad cars shall be checked for breaks and weakness before they are driven onto.” – OSHA 1910.178(m)(7)
Ensure the dock plate is positioned and rated to support the weight of the truck and its load. Incorrect positioning can cause dock plates to shift, potentially leading to buckling if they’re overloaded beyond their capacity.
Personnel Falling from Forks
Standing on the forks of a forklift and being elevated should never be attempted by anyone.
While it may be tempting for convenience’s sake, the chance of falling is extremely high.
Head trauma, broken bones, internal bleeding, and even impalement can happen in personnel who choose to “ride the forks.”
Main Causes of Personnel Falls
- Prioritizing speed and convenience over safety.
- When aerial lifts are unavailable, workers may resort to unsafe alternatives.
- Unapproved or unrestrained lifting platforms.
How to Prevent Personnel Falls
Do not cut corners and slow down. Take the time to select the right tools for the job, even if it takes extra time.
Use the proper equipment. A scissor lift, man lift, or other purpose-built mobile elevating work platform (MEWP) are far better options for safely reaching heights.
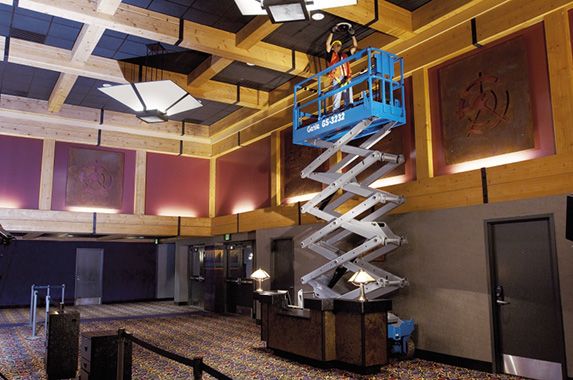
Use OSHA-approved lifting cages with guardrails and harnesses for personnel safety and ensure the platform is attached to the lift to prevent it from shifting and/or falling.
Blocked Sight
If the lift truck operator can not see where they’re going, it’s a recipe for disaster.
It is not just tall loads that can decrease visibility either.
Operators should know their sides and rear blind spots to avoid product, equipment, infrastructure, and pedestrian collisions.
Main Causes of Blocked Sight Incidents
- Driving forward with tall loads
- Driving with elevated forks
- Not checking blind spots around the lift truck
How to Prevent Blocked Sight Incidents
Only travel in the direction you can see. If you have a tall load on the forks, drive backward until you reach your destination.
Have a colleague act as a spotter. When you can not see forward and driving backward is not feasible, get a coworker to guide you. They can act as a spotter, ensuring safe navigation.
Keep the forks low to the ground. Never drive with an elevated mast. It reduces visibility and can cause the lift truck to become unstable and tip over.
Be aware of tailspin risks, as forklifts steer with the rear axle. If the operator isn’t paying attention to their surroundings, the counterweight can ram into pedestrians, damage products, or even take down an entire storage rack:
Mechanical Failures
Forklifts are just like any other piece of machinery: They require maintenance regularly.
When you neglect forklift maintenance, breakdowns, and safety issues are bound to occur.
Main Causes of Mechanical Failures
- Worn brakes
- Leaks: Fluids on the floor are a slipping and stopping hazard
- Worn or damaged tires
How to Prevent Mechanical Failures
Conducting pre-shift inspections is essential for identifying and addressing issues before forklift operation.
OSHA requires daily inspections to promote safety, helping to detect both major and minor problems.
Addressing these promptly ensures the forklift remains in optimal and safe working condition.
“Industrial trucks shall be examined before being placed in service, and shall not be placed in service if the examination shows any condition adversely affecting the safety of the vehicle. Such examination shall be made at least daily. Where industrial trucks are used on a round-the-clock basis, they shall be examined after each shift. Defects when found shall be immediately reported and corrected.” – OSHA 1910.178(q)(7)
Regularly service your equipment. Sign up for a preventative maintenance (PM) program from a quality service center and keep to it.
Pull equipment from service until any issues are corrected. If problems are found, do not operate the lift. Lock and tag the truck out and schedule the repairs.
Emissions Poisoning
While battery-powered forklifts are steadily becoming the preferred choice for many businesses, internal combustion (IC) forklifts are still widely used.
Fortunately, advances in emissions technology over the years have led IC lift trucks to produce fewer and fewer emissions.
However, operating these kinds of trucks can still present hazards to employees.
Causes of Emissions Poisoning
- Operating in confined spaces
- Poor ventilation
- Excessive idling
- Incorrect fuel mixture
- Leaking exhaust
How to Prevent Emissions Poisoning
Ensure operators are aware of the risks of confined spaces. Using lift trucks in storage sheds, semi-trailers, and small rooms can cause a quick build-up of lethal carbon monoxide (CO) gas.
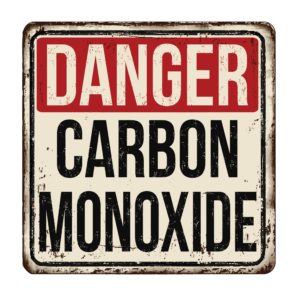
Install ventilation systems. These will circulate the air and help remove gases.
Install carbon monoxide monitors. These can alert everyone in the area to dangerous gas build-ups and give time to evacuate.
Schedule regular maintenance. Maintenance routines should include exhaust checks and fuel mixture adjustments during routine maintenance.
Crushed by Forklift
Crushing hazards are a leading cause of forklift-related injuries and fatalities for pedestrians.
Pedestrians can become pinned between the truck and a fixed object if the operator isn’t paying attention – with often fatal results.
Main Causes of Crushing Accidents
- Inattentive backing
- Crushed by the mast while tilting
- Loose materials falling off the forks
How to Prevent Crushing Accidents
Look before putting the truck into motion. Operators should scan their surroundings, especially behind them, before the forklift gets into gear and moves.
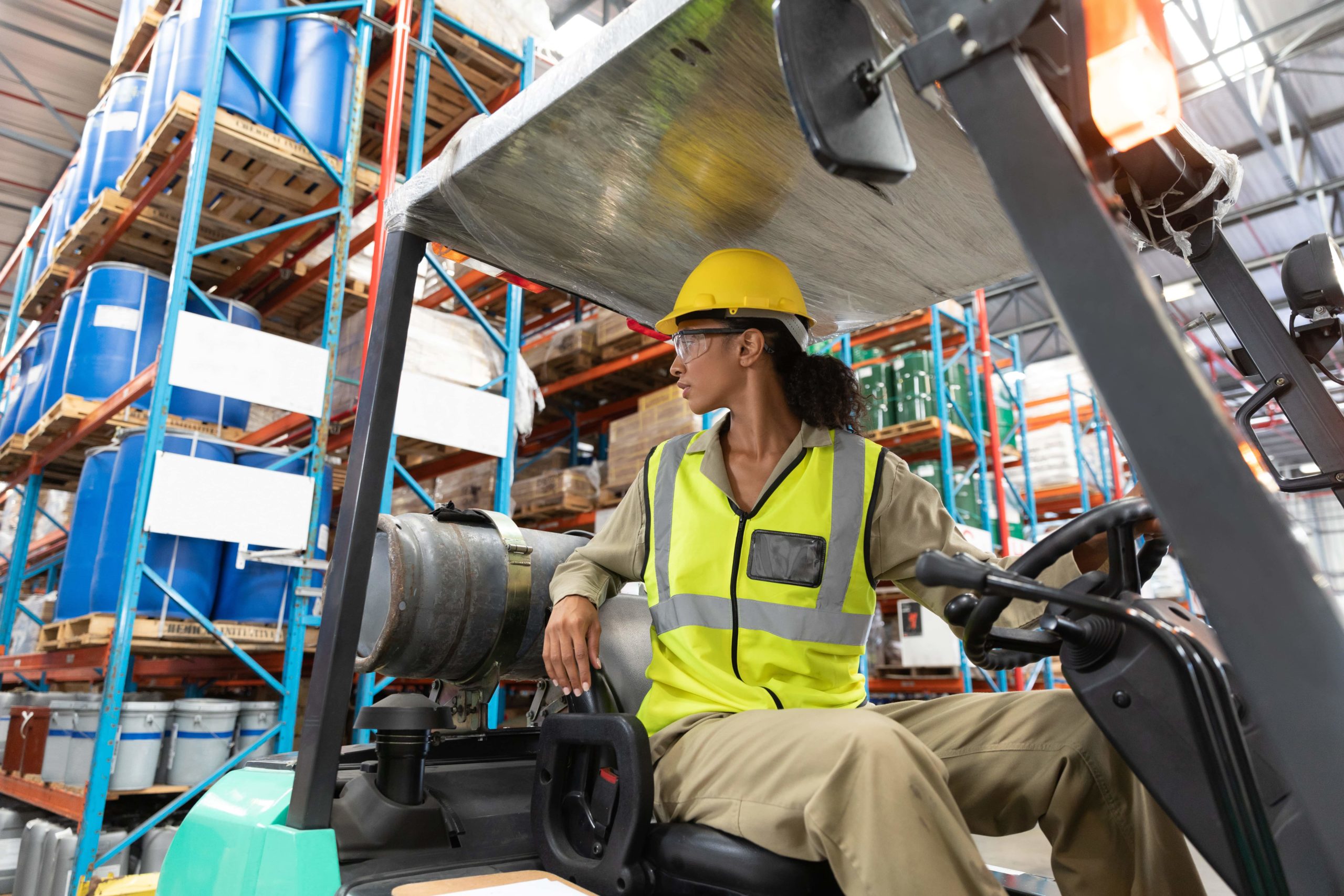
Never drive up to a pedestrian standing next to a fixed object. If the brakes fail or the floor is wet, the truck will crash into the pedestrian, crushing them in the process.
Never leave the operator’s compartment during the operation of the truck. Do not put body parts inside or between the mast and the firewall.
Properly secure the load. Heavy or awkward loads can come loose, landing on pedestrians or the operator.
Legal and Financial Implications of Forklift Accidents
Forklift accidents not only lead to serious injury but legal and financial problems for businesses, operators, and victims.
Knowing these risks and how to address them is crucial if you want to avoiding long-term issues.
Legal Claims and Compensation
Victims of forklift accidents can and often will seek compensation for their injuries.
These claims usually depend on proving negligence, such as:
- Inadequate operator training
- Improper maintenance
- Failure to follow standard safety measures
Once negligence is proven through legal procedure. Victims are rewarded compensation which can include:
- Medical expenses: Covering past and future treatment costs.
- Lost wages: Reimbursement for income lost during recovery.
- Pain and suffering: Damages for physical and emotional trauma.
- Wrongful death: Support for families, including funeral costs and loss of financial stability.
Employers are often held responsible for accidents caused by untrained operators, broken equipment, or unsafe conditions like blind spots or uneven ground.
However employers are not always the ones held responsible for an accident.
In some cases, claims may even target equipment manufacturers if a design flaw causes accidents like rollovers or falling loads.
Financial Costs
Forklift accidents can lead to financial losses that go beyond an initial medical bills.
Victims of a forklift accident may be dealing with long term effects such as:
- Ongoing care: Rehab, therapy, and special treatments
- Lost earnings: Temporary or permanent inability to work
- Property damage: Costs to fix or replace equipment and inventory
Other expenses on the businesses side of the accident include legal fees, OSHA fines, higher insurance premiums, and lost productivity due to downtime.
Emotional and Psychological Effects
Forklift accidents don’t just cause physical injuries—they also affect emotional well-being. Victims and families may struggle with:
- Emotional stress: Anxiety, depression, and trauma
- Family challenges: Financial strain affecting relationships
Providing mental health support is essential and can go a long way in assisting the victim in their recover from an accident.
Reducing Risks and Costs
Proactive steps can and should be taken to help prevent accidents and limit legal and financial consequences.
Previously we covered in depth on how to prevent common accidents, however in a general scope, businesses should:
- Train operators thoroughly
- Regularly inspect and maintain equipment
- Use safety tools like backup alarms, load backrests, and mirrors
- Follow OSHA regulations to avoid fines and lawsuits
In the event of a forklift accident, nobody wins.
So it is crucial to establish strong procedures to prevent an accident, address legal considerations, ensure fair compensation for victims, and protect the business from significant harm.
By addressing these risks, companies can protect employees, reduce costs, and create a safer workplace for everyone.
Forklift Accident Statistics
Now that you know the most common forklift accidents, let us dive into the figures.
However, it’s worth noting that the statistics on workplace mishaps involving forklifts can be somewhat inconsistent.
Nonetheless, we have compiled data from reputable sources, including:
- U.S. Bureau of Labor Statistics
- Occupational Health and Safety Administration (OSHA)
- National Institute for Occupational Safety and Health (NIOSH)
- National Safety Council (NSC)
How Many Forklift Accidents Happen Every Year?
OSHA’s most recent estimates indicate that between 35,000 and 62,000 injuries occur every year involving forklifts.
The U.S. Bureau of Labor Statistics reported that in 2017, 9,050 forklift-related injuries caused employees to take time off work. In 2018, that number went down to 7,940.
Forklift injuries tend to be more serious compared to other workplace injuries. The median number of days off work was 13, compared to 8 days for all other cases.
And when you consider that each injury that requires medical attention costs companies an average of $41,000, it’s clear how high both the human and financial costs are for forklift accidents.
How Many People Die in Forklift Accidents?
About 75 to 100 workers are killed annually in forklift accidents, with a rough average of 87 deaths per year.
Here are the exact numbers for years where the data was available:
- 1980-1994: 1021 deaths
- 1995: 94 deaths
- 2011-2017: 614 deaths
- 2015: 96 deaths
- 2017: 74 deaths
- 2018: 85 deaths
What Percentage of Forklift Accidents Involve Pedestrians?
While the exact numbers fluctuate year to year, forklift accidents involving pedestrians are nearly always at the top of the list.
Data from 2017 provided by the U.S. Bureau of Labor Statistics shows that pedestrians were involved in 20% of non-fatal accidents and 13% of fatal ones.
Here’s the full breakdown of forklift accidents by type:
Forklift Safety: The Human and Business Costs
The infographic below summarizes how much forklift accidents cost in human and business terms.
Conclusion
Forklift safety is everyone’s responsibility.
By understanding common accidents, their causes, and prevention strategies, workplaces can significantly reduce risks, protect employees, and maintain productivity.
Whether it’s proper training, implementing safety measures, or regular maintenance, every step counts.
Interested in taking safety to the next level? Contact Conger today to enhance your forklift operations and prioritize a safer workplace.